Najważniejsze informacje:
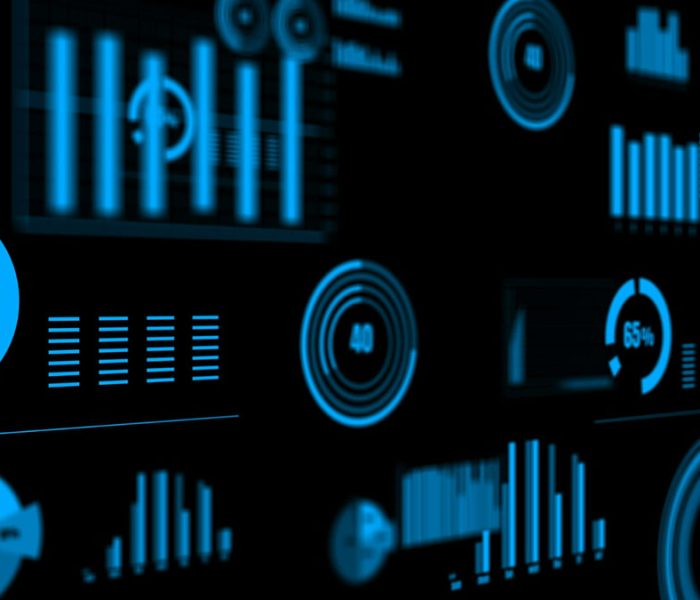
Liczy się jakość danych wsadowych które stają się podstawą do analizy
Moc systemów Genearative AI i przystępność ich zastosowania w codziennym życiu sprawiają, że stają się one siłą napędową najbardziej zaawansowanych technologicznie gospodarek. W naszym przekonaniu istota tych rozwiązań polega na możliwości analizy naprawdę ogromnych ilości informacji, aby na ich podstawie wnioskować o sytuacji bieżącej lub przyszłej.
Problemem w pracy z systemami AI może jednak stać się zagadnienie jakości danych, które stają się podstawą do analizy. Jeśli zadbamy o to, aby dane były na odpowiednio wysokim poziomie, to możemy być pewni, że modele prowadzące do wnioskowania zadziałają w sposób właściwy, prognozując na podstawie zdefiniowanego algorytmu.
W przypadku danych niepewnych, czy wręcz fałszywych, rezultaty takiego wnioskowania mogą być niezgodne z rzeczywistością, a nawet w skrajnych przypadkach niebezpieczne. Zalecamy więc dużą ostrożność w pracy z systemami analitycznymi podyktowaną troską o jakość danych wsadowych, które są siłą sprawczą decyzji systemowych.
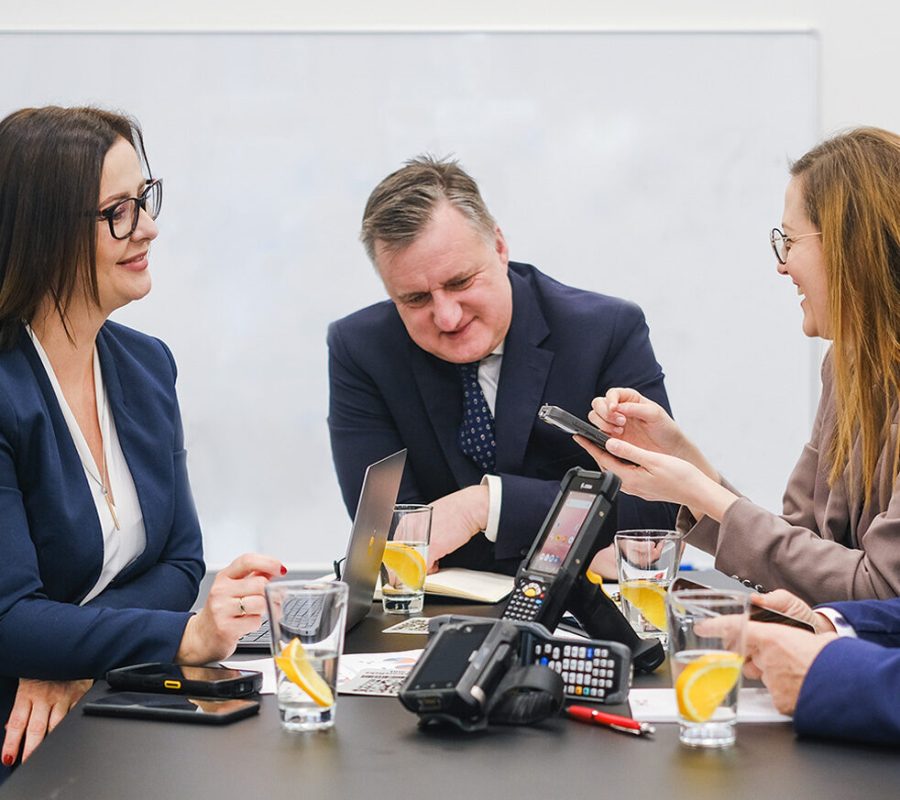
Potencjał i szanse na bezpieczne wykorzystanie systemów uczących się
Specjaliści HKK Group szukają możliwości zastosowań elementów generatywnej sztucznej inteligencji wszędzie tam, gdzie tkwią nasze kluczowe kompetencje, czyli w świecie logistyki produkcji. Modelujemy systemy wspomagania decyzji w naszym systemie WMS, zwłaszcza w obszarze doboru najskuteczniejszych metod kompletacji.
Pracujemy również nad zastosowaniem modeli cyfrowego bliźniaka dla procesów produkcji, w celu umożliwienia dogłębnej analizy alternatywnych przypadków decyzji. Celem jest odnalezienie optymalnego scenariusza, bez konieczności wpływu na realne środowisko produkcyjne czy logistyczne.
Nasze działania korespondują z jedną z podstawowych kompetencji naszych Konsultantów, a mianowicie z obszarem automatycznego zbierania danych.
Takie unikalne zestawienie specjalizacji (z jednej strony zbiór danych, z drugiej zaś możliwość programowania algorytmów decyzyjnych, działających na bazie zebranych wcześniej danych) sprawiają, że systemy, które projektujemy wnioskują na bazie danych najwyższej jakości, co pozytywnie wpływa na możliwości ich użycia w środowisku produkcyjnym.
Systemy które projektujemy wnioskują na bazie danych najwyższej jakości, co pozytywnie wpływa na możliwości ich użycia w środowisku produkcyjnym.Mowa tu o rozwiązaniach typu WMS, Digital Twin i automatycznej identyfikacji.
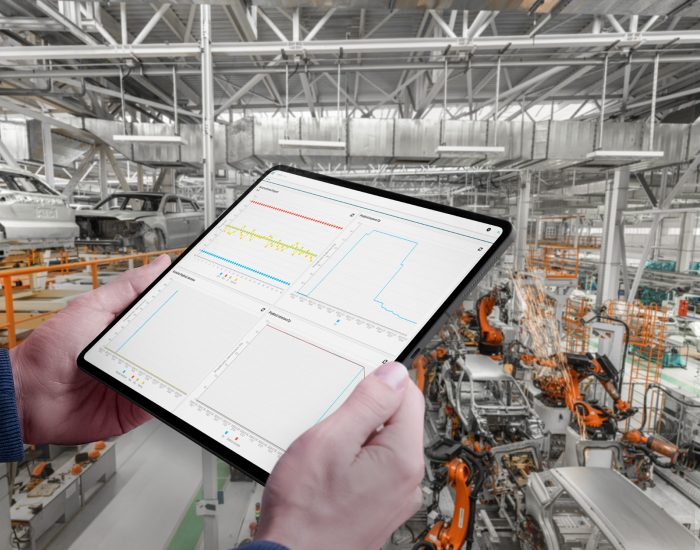
Trochę praktyki - inteligentne sterowanie produkcją w systemie DigitIO
W systemie wspomagającym kreowanie DT (kreowanie decyzji), decyzje dotyczące jakości procesu wytwarzania podejmowane są na podstawie danych dostarczanych z kontroli realizowanej on-line oraz in-line, a w szczególnych przypadkach po zakończonej operacji (off-line).
W swoich założeniach pakiet metod pozwala na analizę danych takich jak: właściwości wyrobu, parametry procesu, sygnały diagnostyczne towarzyszące procesowi oraz zdarzenia, jakie nastąpiły w trakcie jego trwania. Zbiór takich danych stanowi punkt wyjścia do tworzenia modelu stanu procesu, na podstawie którego prognozowane są przyszłe jego stany oraz podejmowane decyzje korygujące.
Z punktu widzenia analizy istotne było ustalenie struktury danych w Module Analizy Danych (ozn. MAD). Została ona pokazana na rysunku nr 1 umieszczonym poniżej.
Rysunek 1. Idea struktury danych w MAD
Dane, na podstawie których wykonywane są analizy w MAD podzielono na 6 głównych klas, o nazwach:
- Właściwości wyrobu – to klasa właściwości związana z wyrobem/elementem/materiałem obrabianym. Przykładowo: średnica szlifowanego elementu, zawartość węgla w materiale, liczba rys na powierzchni obrabianego materiału i inne.
- Wielkości procesowe – to cechy związane z nastawami maszyny oraz sygnały towarzyszące procesowi. Przykładowo: prędkość skrawania, posuw piły, temperatura suszenia i inne.
- Operator – cechy związane z operatorem obsługującym maszynę.
- Zdarzenia – zdarzenie, które ma miejsce podczas realizacji procesu. Przykładowo: wykruszenie ostrza narzędzia, stępienie narzędzia, spadek napięcia w sieci, itp.
- Parametry otoczenia – to właściwości związane z otoczeniem. Przykładowo: temperatura otoczenia, wilgotność, przepływ powietrza w pomieszczeniu itp.
- Wskaźniki produkcyjne – to wartości wskaźników produkcyjnych związanych z aktualnym stanem zlecenia. Np. OEE, wydajności, poziom niezgodności, czas taktu itp.
Moduł Analizy Danych (ozn. MAD) systemu Digit.IO został podzielony na trzy zbiory narzędzi: monitorowanie, prognozowanie i modelowanie.
Na rysunku kolejnym przedstawiono narzędzia analityczne, które zawarte są w każdym z modułów. Wyniki użycia poszczególnych narzędzi są zapisywane w bazie danych i mogą być wizualizowane na Pulpicie Analizy Danych (ozn. PAD).
Rysunek 2. Grupy narzędzi w Module Analizy Danych
Pierwsza grupa narzędzi (rysunek 3) pozwala na monitorowanie wartości właściwości wyrobu, wielkości procesowych, zdarzeń, parametrów otoczenia oraz wskaźników produkcyjnych. Ich rola sprowadza się do pobrania sygnału, ewentualnego obliczenia wskaźnika i zaprezentowania wyniku w formie liczbowej lub graficznej (np. wykresu lub ikony).
Operatora:
- Liczba wyprodukowanych sztuk w danej jednostce czasu przez danego operatora
- Liczba braków pojawiająca się na kolejnych zmianach operatora
Zdarzeń:
- Informacja o zdarzeniu
Parametrów otoczenia:
- Aktualna wartość parametru
- Wykres szeregu czasowego dla wartości parametru
Wskaźników produkcyjnych:
- Aktualna liczba jednostek wytworzonych
- Czas od uruchomienia zlecenia
- Aktualna liczba jednostek do poprawy
- Aktualna liczba braków
- Średni czas produkcji/obróbki jednej sztuki
W tej grupie narzędzi znalazły się dla:
Właściwości wyrobu:
- Statystyki opisowe właściwości
- Wykres szeregu czasowego dla właściwości z określoną częstością
- Wskaźniki zdolności jakościowej Cp, Cpk
- Wskaźniki zdolności jakościowej Pp, Ppk
- Przedziały ufności dla wskaźników zdolności jakościowej
- Wskaźnik ppm/ DPO/ DPMO/poziom sigma
- Rozkład wartości cechy w formie histogramu
- Analiza normalności rozkładu prawdopodobieństwa cechy
- Karty kontrolne do monitorowania stabilności
Parametrów procesu:
- Bieżące wartości parametru
- Wykres szeregu czasowego dla wartości: parametru (np. nastaw maszyny) lub sygnałów diagnostycznych z procesu (np. siła, drgania)
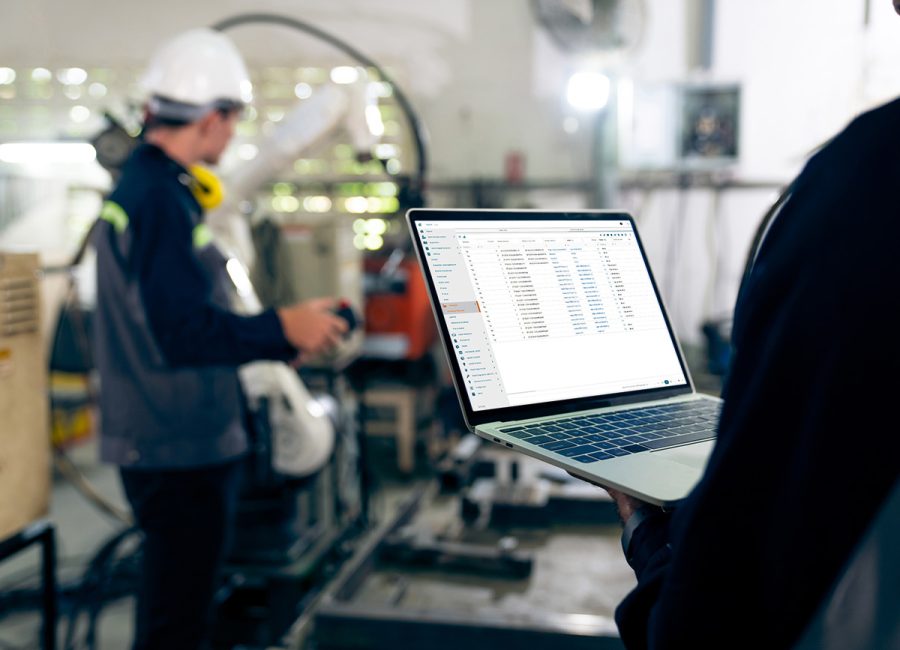
Drugą grupę narzędzi stanowią narzędzia prognozowania (rysunek 2). W tej grupie zaprojektowano wykonanie prognoz w oparciu o analizę szeregu czasowego dla wartości właściwości wyrobu, sygnałów diagnostycznych oraz zdolności procesu.
Trzecia grupa narzędzi służy modelowaniu pozwalającemu na wykonanie analizy zależności pomiędzy cechami. Celem modelowania jest wskazanie dla jakich wartości parametrów procesu, otoczenia, zdarzeń otrzymamy oczekiwaną jakość wyrobu.
W tym celu zaprojektowano zastosowanie analizy regresji, sztucznych sieci neuronowych oraz drzew decyzyjny w odkrywaniu zależności pomiędzy zmiennymi zależnymi a jakością wyrobu
Narzędziem będącym klamrą dla trzech grup jest autorski algorytm nadzorowania i prognozowania zdolności jakościowej procesu wielostopniowego procesu wytwarzania, który pozwala na wyznaczenie ryzyka niespełnienia założeń procesu związanych np. z przepływem produkcji. Ryzyko to wyrażane może być jako prawdopodobieństwo lub liczba jednostek, które będą wadliwe lub brakiem. Informacja ta przekazywana jest do modułu planowania przepływu produkcji celem, o ile to niezbędne, zmiany planu produkcji.