Digital Twin - a digital twin for production control
Advanced scheduling, statistical analysis and production forecasting. Introducing the digital twin of your factory.
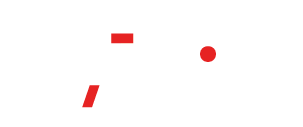
01/
Artificial intelligence and IoT
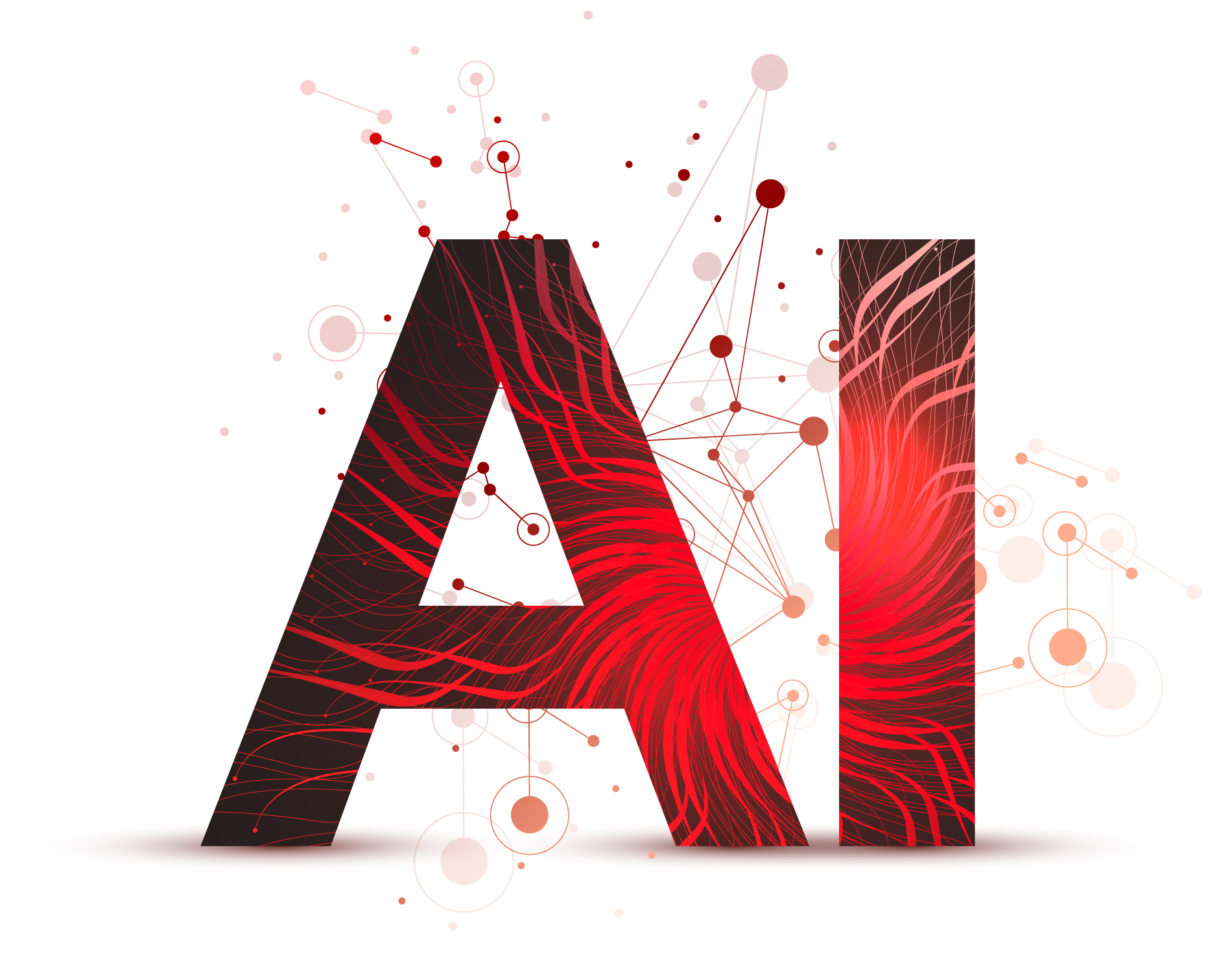
Today's production hall is the meeting place of modern technology.
Strategic decisions are worth supporting with artificial intelligence algorithms with the help of the Internet of Things.
From sensors that measure every aspect of machine operation, to intelligent algorithms that suggest the best solution to problems that arise during production.
The flow of information related to processes should be instantaneous in order to be able to adjust production parameters in real time to the events taking place on the shop floor. Their analysis should be automated, suggesting the best off-the-shelf solutions to managers.
02/
Digital Twin concept
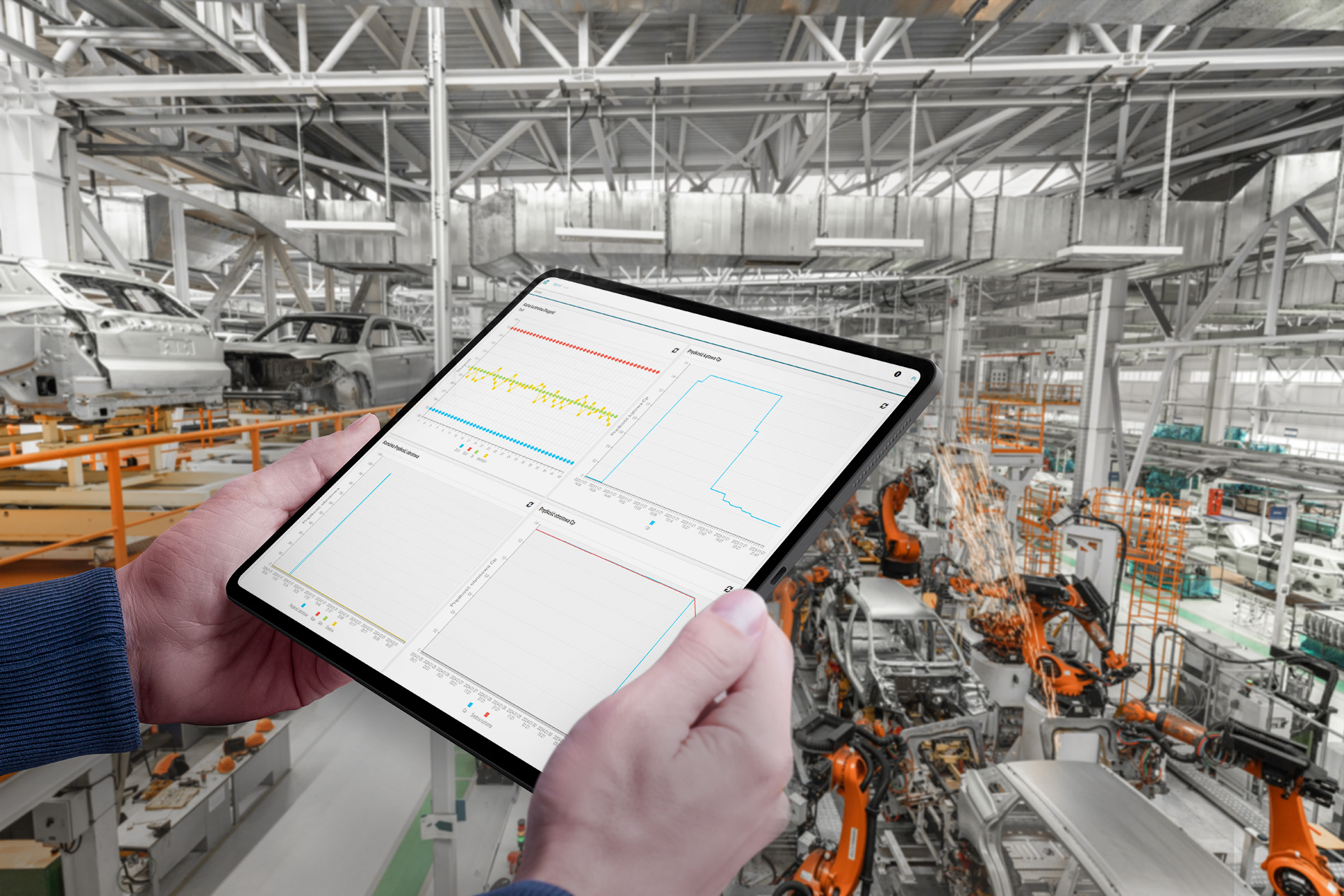
Digital Twin is a faithful digital reflection of reality in a selected area. In the case of the Digit.IO Factory system, it is a reflection of the production process
Our system consists of an invisible but crucial backend layer and a visual representation of the production floor, which is also the user interface.
By applying this concept, it is possible to simulate alternative production scenarios in such a way as to select the best possible one, without the need for real-world testing under production conditions. In this way, digital twin enables process and cost optimization. Using it avoids the risk of implementing solutions that will not work.
03/
Transparent manufacturing
Wanting to control every detail, even the smallest, affecting the speed and efficiency of the production process, it is necessary to reach for the powerful possibilities offered by technology.
This effect will be achieved by supervising devices from the automation area such as sensors, readers and other measuring devices that analyze production processes autonomously and without human involvement. It is also important to keep an eye on the work of operators who operate production machinery. The digital twin allows you to test your solutions in practice, not just on paper. In this way you can, even before their final implementation, learn about the effects, challenges, costs, which will help you avoid misguided investments that project not only the budget, but also the image.
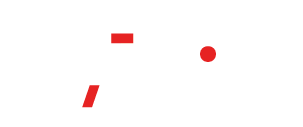
Technologies, schedules, control.
The basis of the Digit.IO Factory system is the production schedule, supporting the manufacture of specific products.
Scheduling itself is intuitive, offering the ability to edit items quickly and easily. With the ability to collect information directly from the production line in real mode, the schedule is matched with real progress, and the collected data can be used to build alternative production scenarios in the digital twin module.
04/
Powered by intelligent algorithms
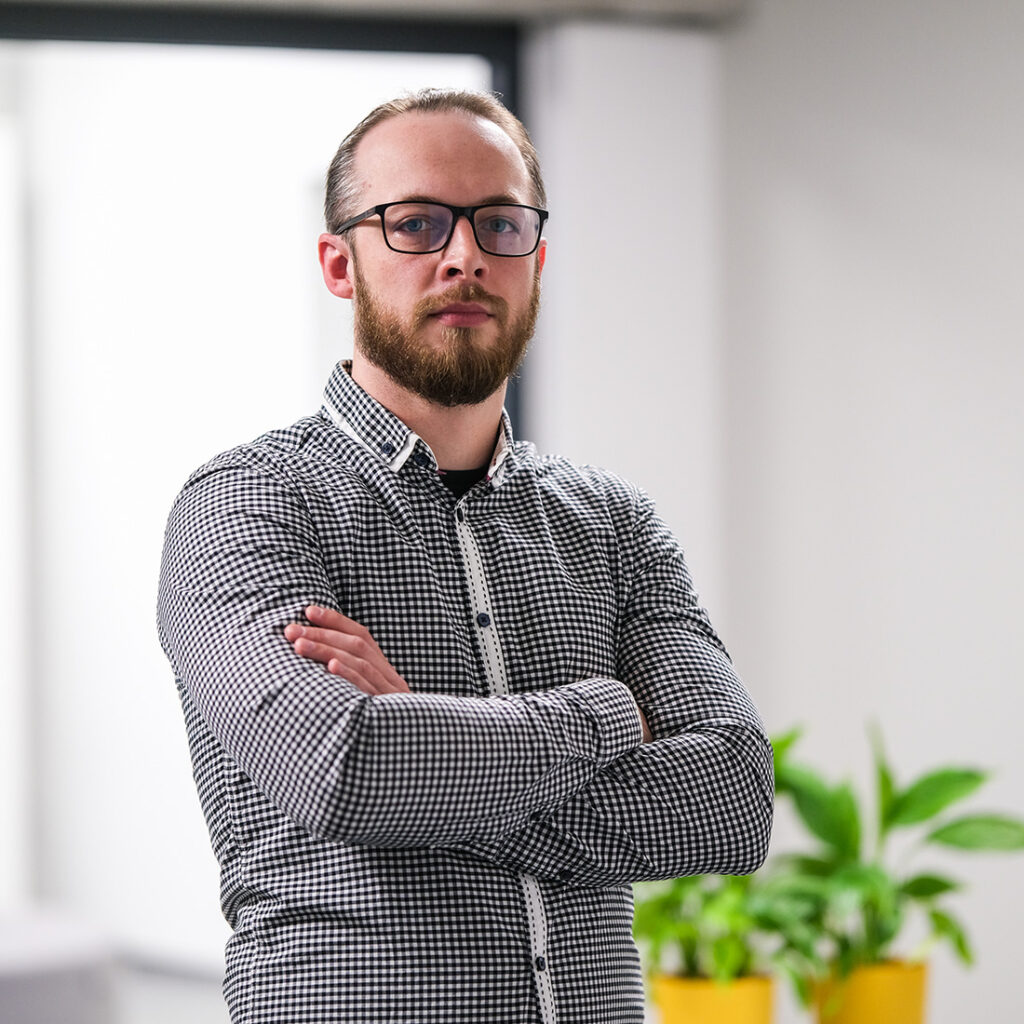
Support key decisions with integrated expert module
It functions on the basis of coded algorithms fed by data flowing directly from the production floor.
The software analyzes alternative production scheduling scenarios to find the optimal one from the perspective of a specific decision criterion. The ability to select the scenarios tested in the digital twin makes production run as smoothly as possible.”
Przemyslaw Luczak
Digit.IO Application Developer
Full system scalability
Digit.IO Factory operates on the basis of modern software solutions, ensuring stability and performance on any device.
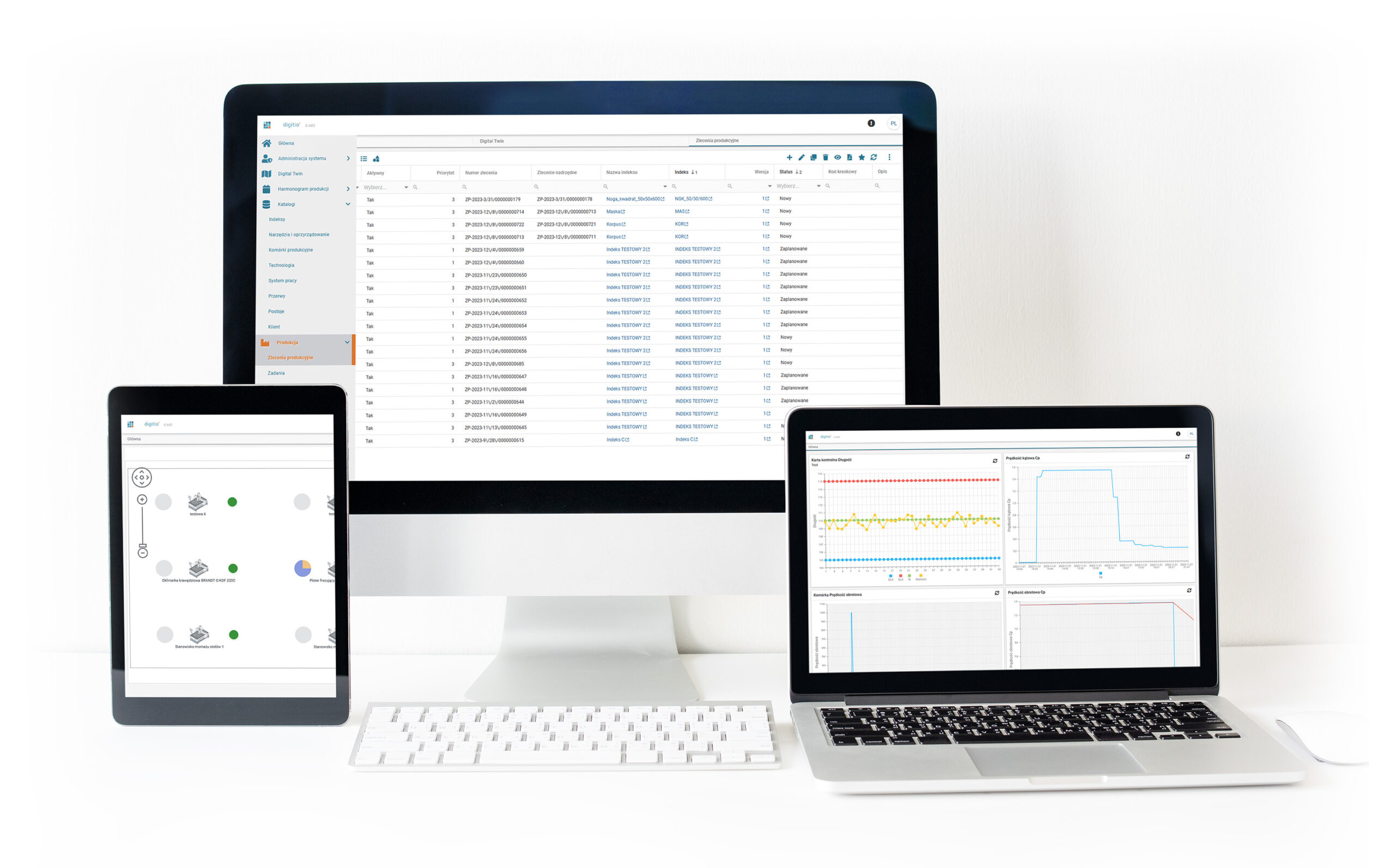
Digital twin - what is it?
Innovative manufacturing companies are increasingly turning to digital twin. What is it? You could answer that only software, another system to manage your business. Meanwhile, a digital twin is real support offered to you by modern technology. And all thanks to artificial intelligence, which accurately collects and analyzes data so that you can make informed decisions.
Do you want to modernize your company, including production processes in particular? Wondering if the developed models will bring the expected benefits? Take advantage of Digital Twin, with the help of which you can easily reproduce your production digitally. The system is intuitive, which makes working with it more pleasant.
Digital twin technology - your business support
HKK Group supports you in your business decisions every day. Digital twin technology is another step towards modernity that you can take together with us. We offer you not only professional products, but also full technical support. If you and your employees have not had any contact with digital twin until now, we will teach you everything.
Wondering which manufacturing processes can be improved through automation? The innovative solutions available in our offer are not only digital twin, with which you will perform simulations. We also offer devices with which you can automate repetitive processes, hitherto performed by humans or only semi-automated.
At HKK Group, we take a holistic approach to our customers, so in our offer you will find products that will enable you to optimize your production, storage and logistics processes. We realize that each company has different needs and requirements, so we try to sew numerous solutions “to measure”.
Do you have additional questions? Get in touch with us!
Digital twin is a technology that has already helped many companies – now it can also support you and your employees! Do you want to test our solutions, or maybe you want to implement them as soon as possible? Feel free to contact us – we will answer all your questions and prepare an offer tailored to your company. Find out today how a digital twin can help your company strengthen its position on the market!
What about production logistics?
Use the WMS
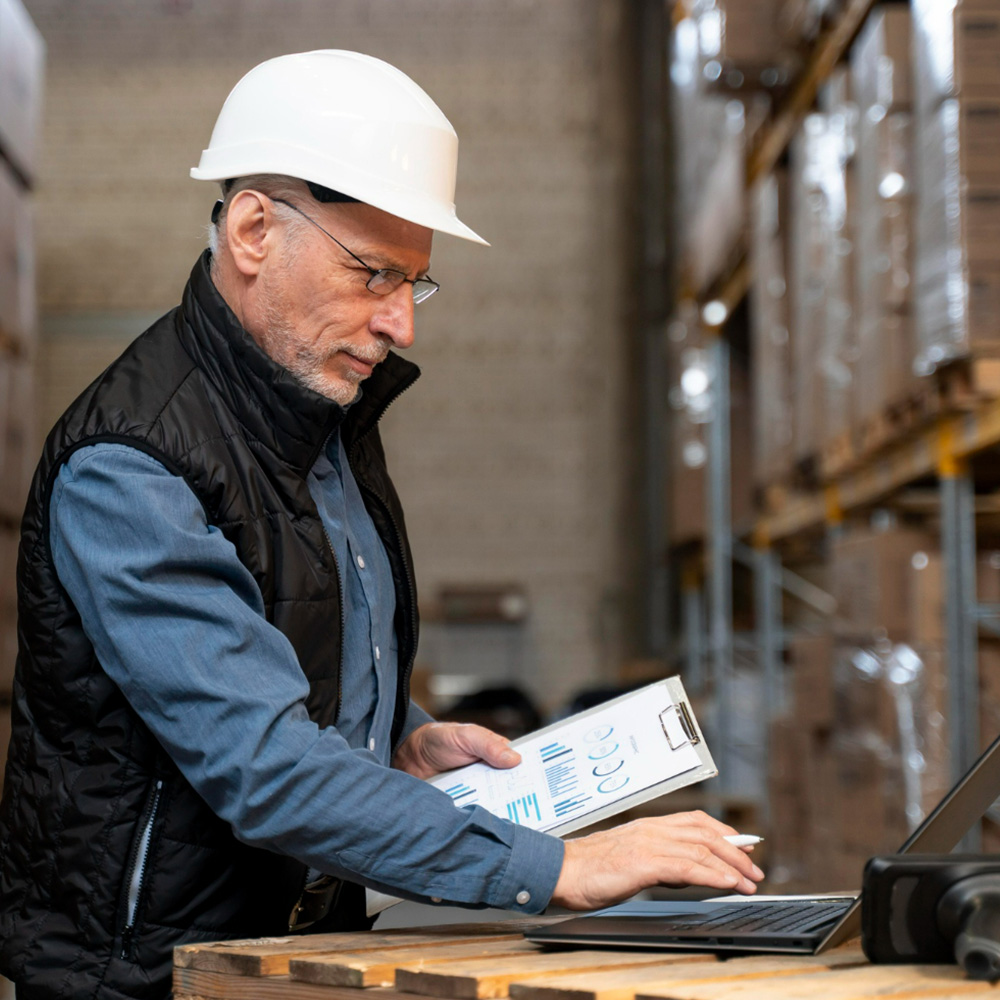
Digit.IO, is an innovative platform for supporting manufacturing processes.
In addition to the scheduling segment, the system offers the possibility of comprehensive support for all production logistics.
Digit.IO WMS is a component of the system that supervises the control of the supply of production components directly to the line, or production nests, using automatic identification technology (bar codes, 2D codes, RFID) and elements of automation and robotics (AGV robots).
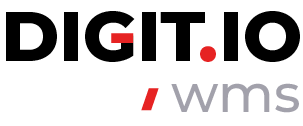
Management based on accurate and timely data.
Digit.IO Control software
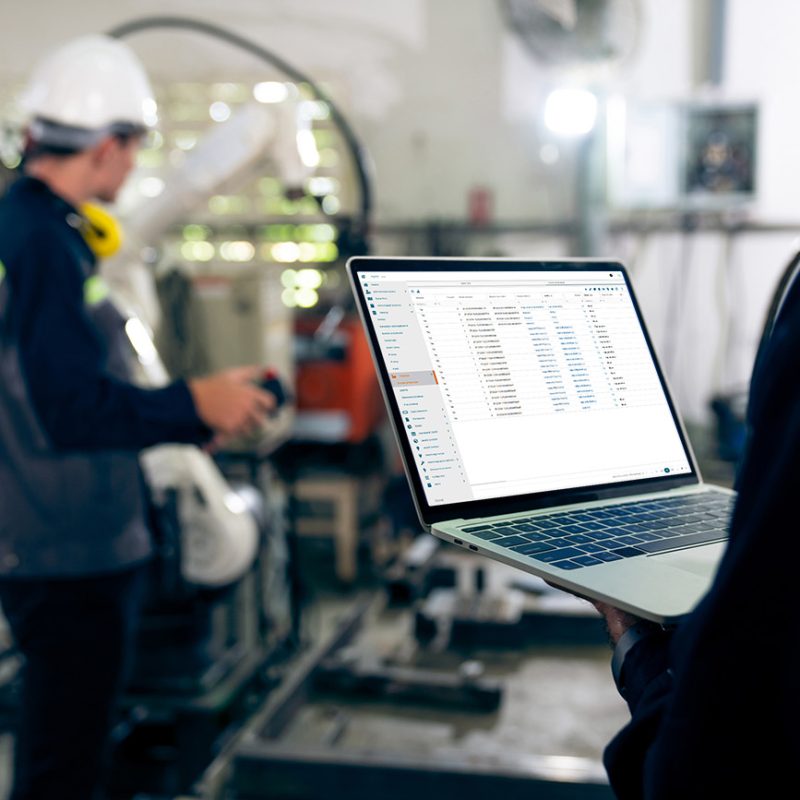
Digit.IO Control is an advanced manufacturing process analysis software .
This is based on data extracted online from processes related to product manufacturing and the flow of materials in the factory.
Through the use of statistical tools, it is possible to identify deviations and risks in the implementation of processes and forecast its future state. This makes it possible to manage on the basis of appropriate and optimal operational decisions.
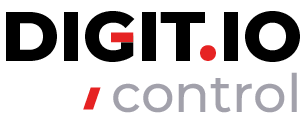
Automation for logistics and manufacturing
We will design and implement automation systems in your enterprise.
In a world of rising employment costs and ongoing shortages of skilled personnel, it is becoming essential to reach for process automation solutions. In order to properly identify the potential for automation, look for task repetition. If the work in certain areas bears such hallmarks, it is very likely to be automated. Our offerings include:
05/
Joint forces, means more opportunities
HKK Group, being the leader of the consortium, has obtained a grant from the National Center for Research and Development for the implementation of a research project entitled “The Future of the HKK Group”. Development of an information system for active production control using the Digital Twins concept.
The project is implemented under Measure 1.1 of the Operational Program Intelligent Development 2014-2020, co-financed by the European Regional Development Fund.
The aim of the project is to develop a new innovative product in the form of an IT system that enables active production control through dynamic production scheduling and ongoing monitoring of material flow parameters and manufacturing processes. Operation of the system will be based on analysis and decision-making using simulation and decision support methods. The work will be carried out by a consortium consisting of: HKK Group and Consortium: Faculty of Mechanical Engineering of Poznan University of Technology. The project is divided into 5 phases.
The result of the project will be: an information system in line with the Digital Twins concept. The system’s functional solutions will allow digital reproduction of real production processes.
POIR.01.01.01-00-0352/21
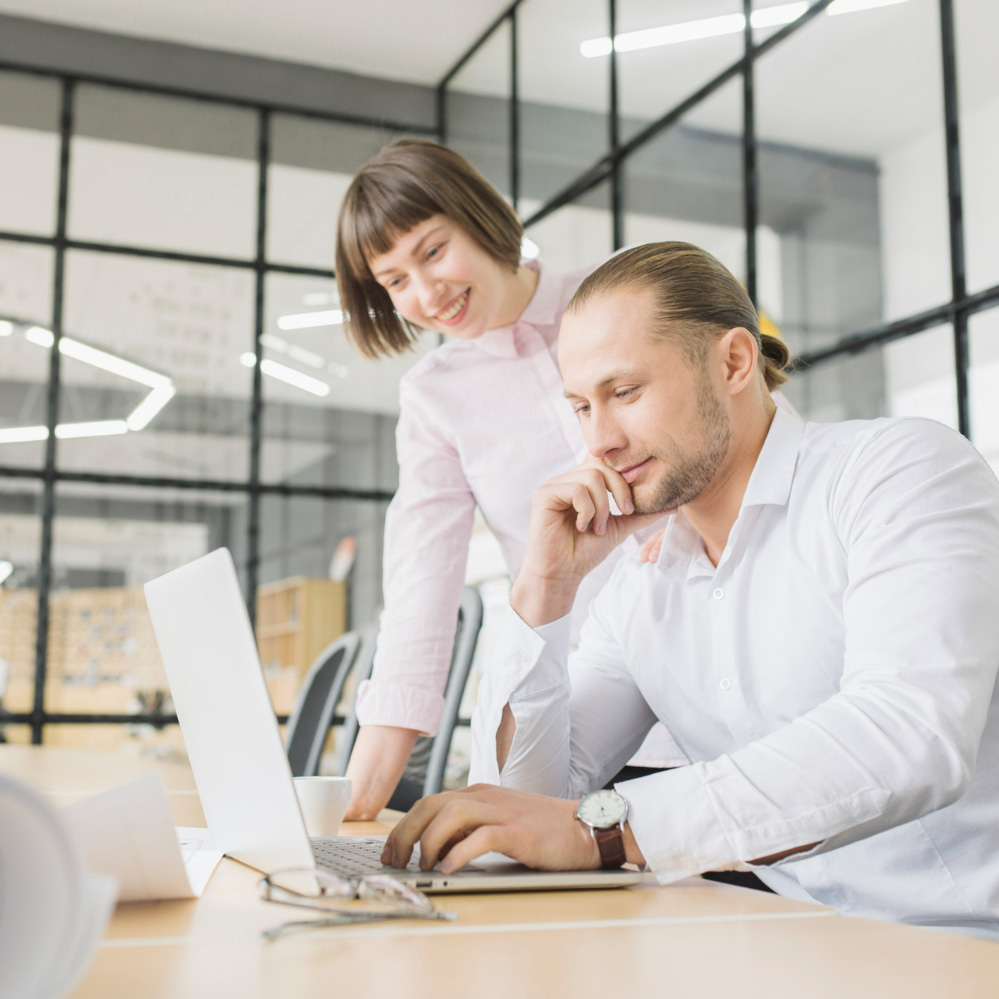
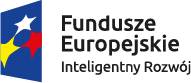
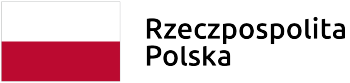
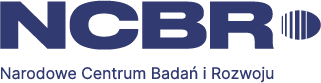
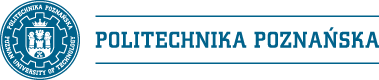
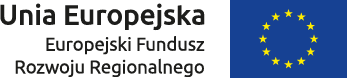
Consulting and optimization services
Close cooperation with the Poznan University of Technology enables us to offer professional advice on improving management processes and production organization.
06/
Contact with us
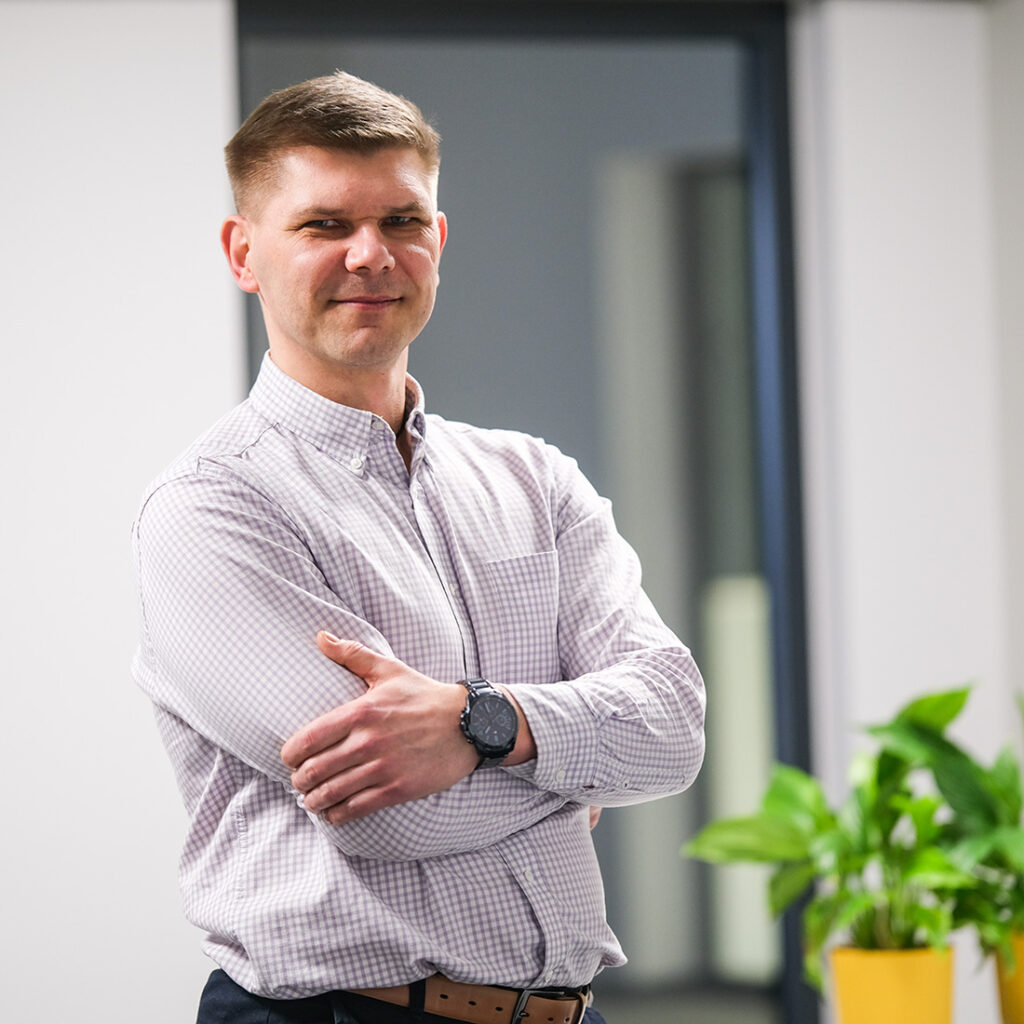
Sebastian Lisowski
Customer Advisor - Digit.IO Systems
Sebastian is passionate about new technologies, especially those supporting complex production and logistics processes. With his well-known commitment and a gleam in his eye, he will take on the challenge of even the most difficult optimization projects.
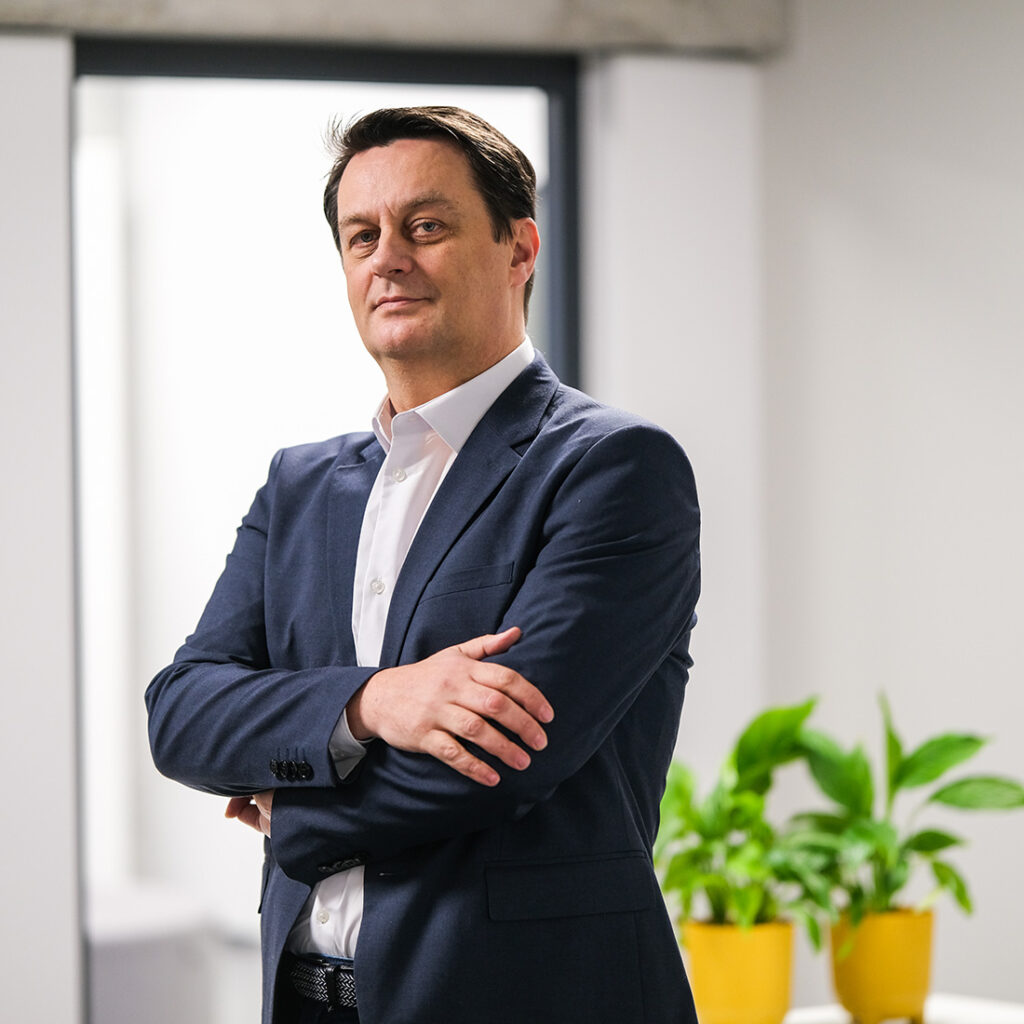
Zbigniew Chudziak
Customer Advisor - Digit.IO Systems
Zbyszek has been in our team for many years. He has carried out thoughtfully dozens of WMS implementations of various scales of expansion. His experience and knowledge are a support at every stage of the project.