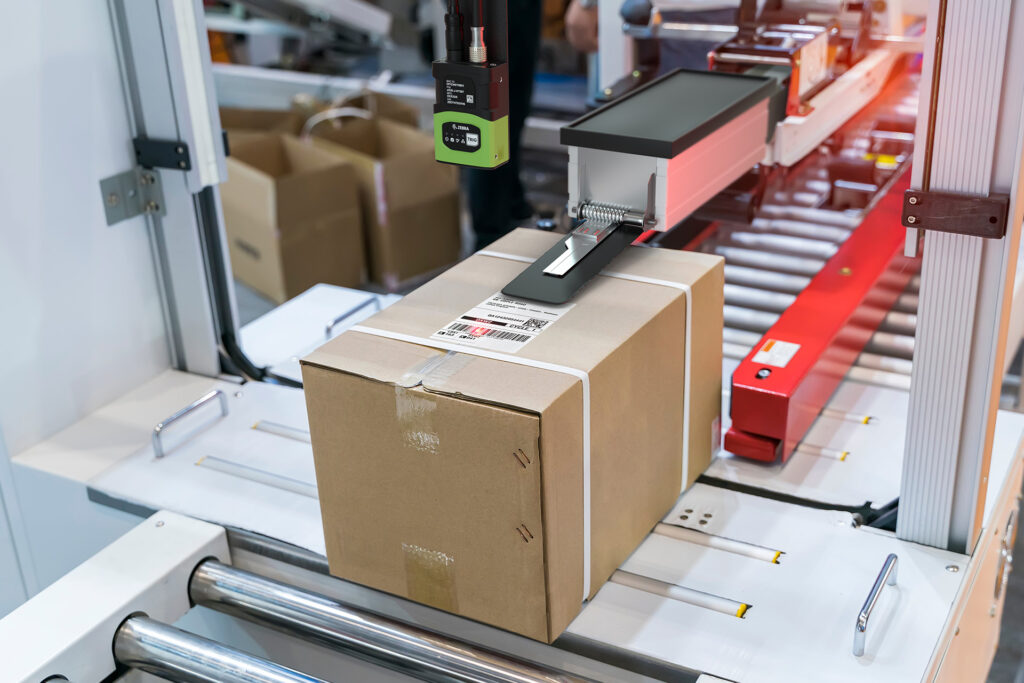
Automatic label applicators – Print & Apply systems
Recent months have brought news of increasingly bold investments in complex systems that automate large areas of warehouse logistics.
Here is a new quality of organization for all key logistics processes.
Thanks to which we get rid of errors with the reading of records, eliminate discrepancies in the interpretation of data and save the time needed to clarify or analyze them, gain a digital footprint of the tasks performed and also eliminate the risk of losing or damaging documents in the course of work.
Speed up the course of warehouse operations and eliminate mistakes. A WMS is a guarantee of getting the right goods to the right customer, at the right time. Thanks to the system, the implementation time for new employees is reduced and existing human resources can be managed more efficiently. You will schedule tasks according to priorities and assign appropriate tools to current tasks.
By integrating with other corporate and customer systems, the WMS increases transparency throughout the supply chain, giving the user the ability to plan inventory and replenish fast-moving goods and the customer a full picture of the degree of order fulfillment.
A WMS is a tool that provides the ability to adapt to changing environments and needs, as well as scalability to the size of the organization. The system can be developed independently, without the need to involve specialists, and the rich standard functionality allows new functions to be launched in no time, which translates into more efficient system implementation and faster configuration.
The technology offered by our company guarantees the possibility of using the functionality for many years, giving you the opportunity to follow the dynamically changing trends in warehouse logistics. The continuous development of our solutions is a guarantee of using best practices.
In a warehouse supported by a WMS, work is simply better. This will therefore translate into better well-being, satisfaction and less stress for employees. You will also gain a reputation by offering competitive terms of employment.
It’s true that there are relatively many WMS offerings on the market. But what makes it worth choosing us?
Mobile terminals, data collectors, tablets, barcode scanners, label printers, RFID solutions, Voice Picking technology, Cubiscan dimensioning devices, building infrastructure for wifi networks.
Marking of high-bay racks with individual number, alphanumeric location marking and barcode or 2D code. End of aisle signs, floor signs, overhead signs and digitally displayed signs. 5S products and health and safety signs. We have our own large-format printing plant.
We operate our own state-of-the-art printing plant for self-adhesive labels and tags. We provide a full range of products through blank labels, product labels, logistics labels, information labels, function labels, variable content labels, and RFID tags.
Blue Yonder WMS is a leader in the global Gartner® Magic Quadrant™ ranking for warehouse management systems. The Blue Yonder warehouse management system enables the efficient implementation of tasks related to warehouse logistics in the largest distribution centers. Our implementation experience is not limited to the Polish market, but extends from the Baltic States, through Western and Southern Europe, to Israel.
We can carry out virtually any implementation ourselves, even the most complex ones.
We have decided to gradually implement the WMS at most of our contract logistics customers - both new and existing. Several important and successfully completed projects are behind us. Each of these involved significant improvements to existing processes, and very often the design of entirely new solutions. This has strengthened our competence in managing the WMS, allowing us to use its capabilities more and more effectively. I can safely venture to say that we have learned the system in such detail that we can carry out virtually any implementation on our own, even the most complicated ones.
Flexibility in solution and pricing, low TCO, and local support.
We need software with a wide range of functionality that can be quickly and seamlessly customized to meet our needs," said Slawomir Pawlak, director of the company's business unit. Raben Group's Information Technology and Telecommunications Department. RedPrairie WMS is a comprehensive and flexible system that will support our operations in many areas of warehouse handling. The company itself provides a sustainable product development concept for post-implementation customer service. We decided on RedPrairie WMS because of the solution's flexibility, pricing, low TCO and local support for logistics tasks.
Overcoming omnichannel's biggest barrier - the automation of warehouse flow processes and the growing stream of returns.
The decision was made to implement the JDA Warehouse Management solution from an omnichannel angle. It supported the operations of the main distribution center for a chain of 62 large-format stores in Poland and the Leroy Merlin sales network in Ukraine and Romania.
The project encompassed 3 basic phases corresponding to Leroy Merlin's main distribution channels: e-commerce, cross-docking (i.e., picking transshipment, which involves handling and shipping goods to the customer directly after delivery to the warehouse, without storage) and stock (warehousing).
The fruits of the implementation include 24 storage strategies, 4 strategies for automatic allocation of goods to orders, 33 independent mechanisms for creating picking lists, several strategies for automatic replenishment of picking locations, and more than a dozen inventory strategies. The use of JDA WMS overcame the biggest barrier of omnichannel - the automation of warehouse flow processes and the growing stream of returns. From there, it's a straight road to "me-commerce" - full integration of channels and modern service offerings that put the customer at the center.
We can confidently recommend the company as a supplier with a professional approach to customers, a comprehensive offer and extensive experience.
With the launch of the new Distribution Center, HENDI Poland decided to streamline internal warehouse processes and implement a WMS-class system for warehouse management. The implementation partner was HIT-Kody Kreskowe, a company with which HENDI Polska had previously cooperated in the purchase of labels and thermal transfer ribbons for label printers.
The project began with an analysis of the company's logistics processes, defining requirements and determining the issue of system integration with the parent system. HIT-Kody Kreskowe provided HENDI Poland with a comprehensive solution by providing all the necessary system components and a range of value-added services, including. the supply and installation of signs and specialized labels for warehouse signage, or the measurement and installation of a WiFi wireless network. The implemented solution provides us with access to up-to-date stock levels, a preview of the actual status of work in the warehouse, and has also allowed us to reduce the time-consuming registration and control of work performed.
We are very satisfied with the implemented system and cooperation with HIT-Kody Kreskowe We can confidently recommend the company as a supplier with a professional approach to customers, a comprehensive offer and extensive experience in its industry.
Recent months have brought news of increasingly bold investments in complex systems that automate large areas of warehouse logistics.
Artificial intelligence, learning systems, logistics automation or AGVs – these are just a selection of buzzwords that have been breaking popularity records in the logistics industry lately.
Customer Experience refers to the set of customer experiences throughout the purchasing process. The evaluation of the purchase consists of a number of factors, at the center of which is, of course, the product itself. An important one is its availability, price, the way it is packaged, or the sheer ease of making a purchase. To be successful here, efficient and modern logistics are necessary.
The area of warehousing has become one of the most important centers of competitive advantage generation in recent years. The modern consumer pays less attention to loyalty to a particular store or brand, and more to availability, price and speed of commercial transaction.
How to deal with time pressure, changing demand, labor shortages and other supply chain challenges? A few words about the digitization of the warehouse made possible by the use of BlueYonder tools.
In today’s e-commerce world, which is growing rapidly especially after the pandemic, returns logistics has gained importance as a key component of customer service. Effective returns management not only allows companies to minimize losses, but also to build customer trust and reduce environmental impact. In this article, we take a look at the challenges of returns logistics, how modern technologies support the process, and how companies can optimize operations to minimize costs and reduce CO2 emissions.
Together with our client, we have set ourselves the goal of implementing Digitio WMS, which is an integral part of the logistics operator along with its components.
Recent months have brought news of increasingly bold investments in complex systems that automate large areas of warehouse logistics.
Artificial intelligence, learning systems, logistics automation or AGVs – these are just a selection of buzzwords that have been breaking popularity records in the logistics industry lately.
Customer Experience refers to the set of customer experiences throughout the purchasing process. The evaluation of the purchase consists of a number of factors, at the center of which is, of course, the product itself. An important one is its availability, price, the way it is packaged, or the sheer ease of making a purchase. To be successful here, efficient and modern logistics are necessary.
Together with our client, we have set ourselves the goal of implementing Digitio WMS, which is an integral part of the logistics operator along with its components.
Sebastian is passionate about new technologies, especially those supporting complex production and logistics processes. With his well-known commitment and a gleam in his eye, he will take on the challenge of even the most difficult optimization projects.
Zbyszek has been in our team for many years. He has carried out thoughtfully dozens of WMS implementations of various scales of expansion. His experience and knowledge are a support at every stage of the project.