Implementation of a WMS system at logistics operator Makana Sp. z o.o.
01/
Customer information
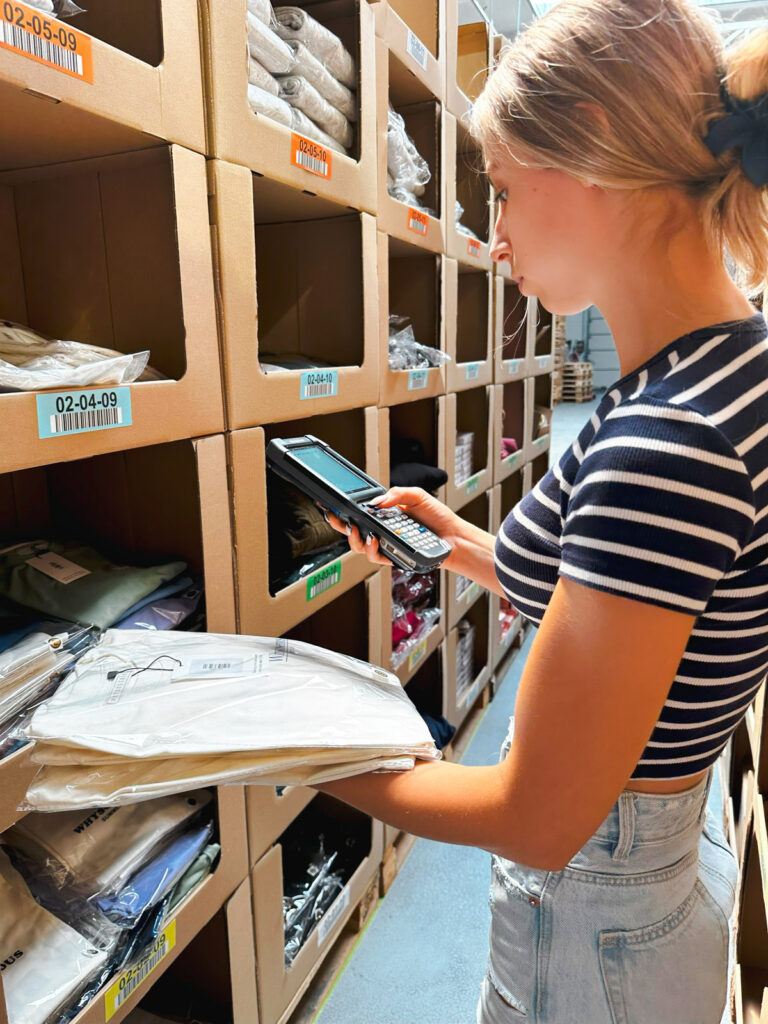
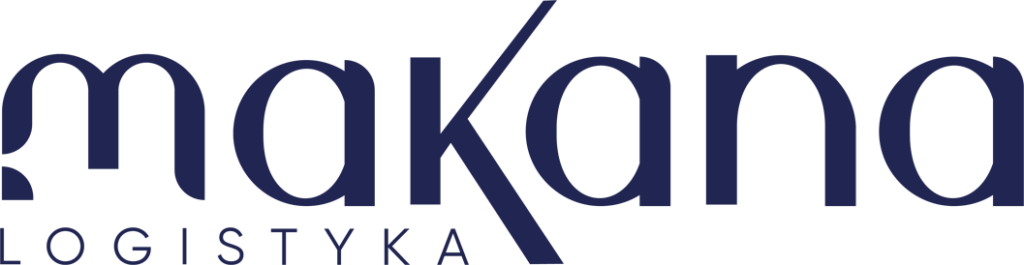
Makana Sp. Ltd. is a growing logistics operator that has been on the market since 2020. An ambitious and young team is dedicated to supporting sellers in e-commerce channels. Makana provides services to small and medium-sized online stores in the apparel, cosmetics, publishing and food industries. The company's idea is to go beyond standards in e-commerce logistics.
The company’s customers can count on professional services in the following areas Warehousing of goods and system support (real-time preview of order processing); VAS (including labeling, co-packing, repacking); order picking (inserts, dedicated packaging); shipping of online orders (wide choice of delivery methods and shipping companies); returns handling (quality control, refurbishment, documentation).
With such an extensive range of products and professional service, store owners can concentrate solely on selling their goods.
- Location: Zielniczki / Środa Wielkopolska
- Industry: logistics operator (fulfillment)
- Website: www.makanalogistyka.pl
02/
Description of implementation
Together with our client, we have set ourselves the goal of implementing Digit.IO WMS, which is an integral part of the logistics operator along with its components.
The implementation was preceded by a thorough analysis of all the client’s warehouse processes.
The main challenges included:
- Lack of data consistency between the stock visible in the ERP system and the actual stock in the warehouse, which negatively affected picking efficiency and order processing.
- System configuration that takes into account the specifics of goods belonging to companies in different industries (e.g., expiration date).
- Optimization of the picking process (speeding up by 30%, reducing errors by 90%).
- Dedicated picking algorithms depending on the specific nature of the goods and the form of delivery.
- Ability to create MOP picking lists for each commodity owner separately.
- Sending the owners of the goods real information about the stock after each operation performed.
System implementation Digit.IO WMS requires the use of location marking for all storage areas.
In this case, cardboard modules that serve as shelving units were mainly labeled.
The advantage of the cardboard modules is their mobility and positioning, which translates into flexibility in constructing the structure of the warehouse.
The labeling included WMS location labels with a barcode and a logical sequence of characters indicating the aisle, column and level of each module.
Goods location codes are read and identified via Honeywell CK65mobile terminals. Thanks to a web-based interface, operation of the Digitio WMS takes place both via the terminals and a PC workstation.
Operators have extensive and precise knowledge of the goods and their attributes , as well as where they are stored in the warehouse.
Attributes are extremely important in the sale of groceries (best-before date), clothing (size, collection) and electronics (serial number), both in order processing and in handling returns.
Advanced algorithms additionally take into account order picking priorities, giving priority in this case to “parcel” orders over parcels picked up by couriers (different pickup times).
Our client has an advanced analytical module that allows the generation of dedicated reports and visualizes relevant information such as the percentage completion of each MOP picking list.
03/
Implemented solutions
04/
Our customer's opinion
You don't have to have a huge distribution center to afford to implement a WMS.
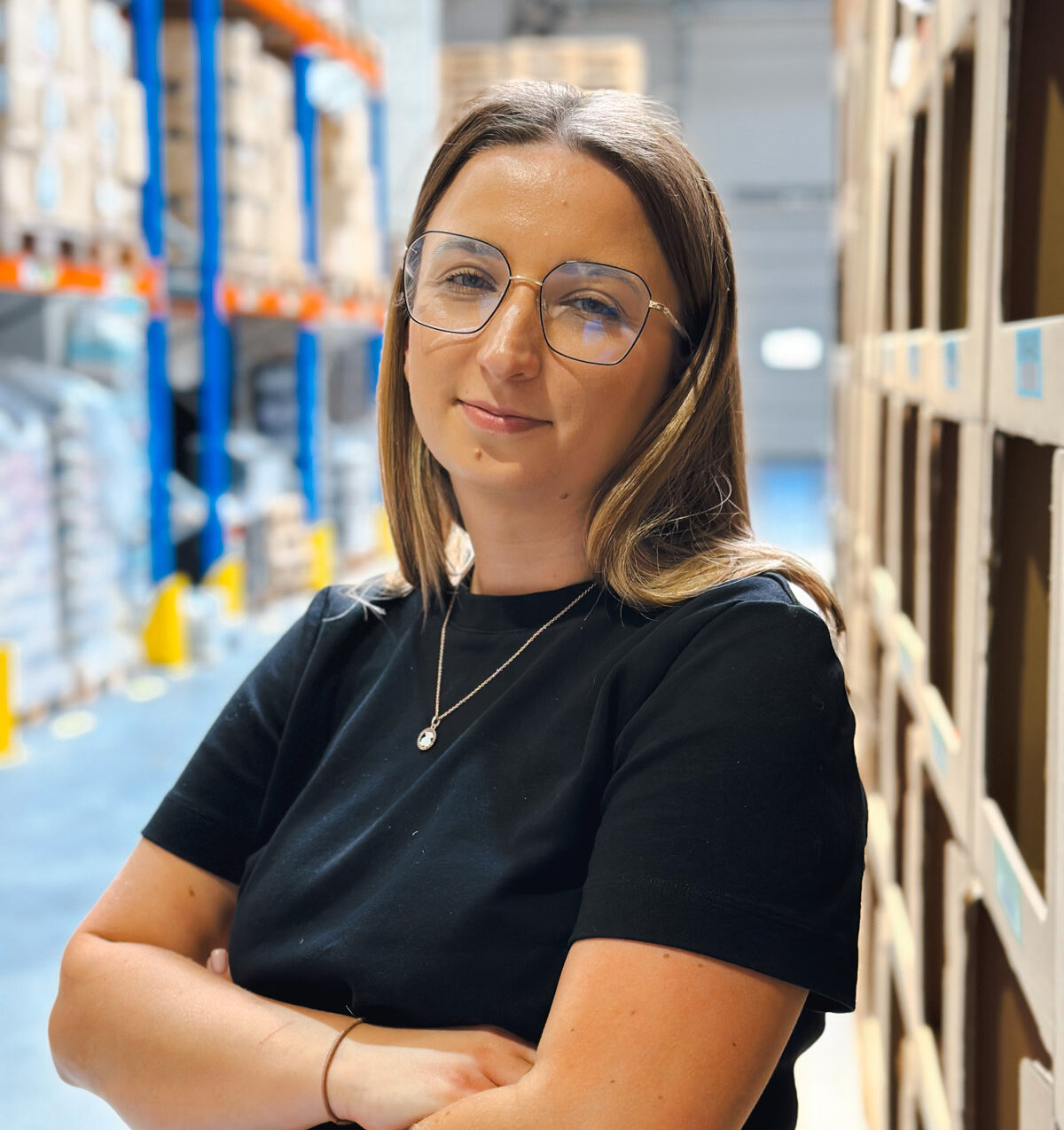
Katarzyna Ratajczak
Makana Sp. z o.o.
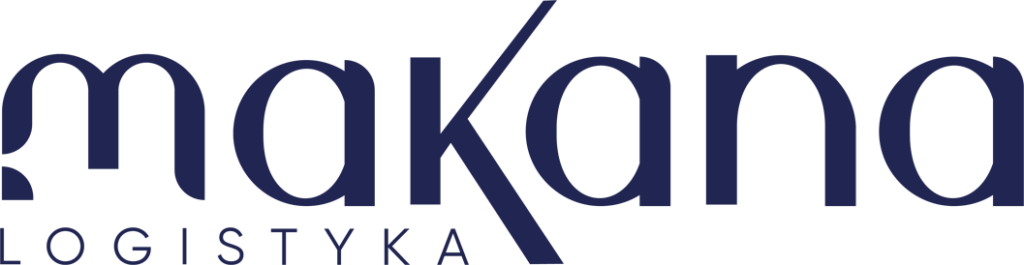
Thanks to Digit.IO WMS our warehouse has undergone a real revolution.
We have streamlined the picking and shipping process, which opens up the possibility of serving more customers.
The introduction of labeling and integration with the e-commerce platform has enabled us to monitor inventory in real time, which has significantly increased our productivity and comfort. The supplied terminals are lightweight, the installed software runs smoothly, and its operation is intuitive and requires only basic training.
It is a myth that systems such as WMS are only for large companies with sizable budgets.
Our business includes small and medium-sized online stores, which is the size of our warehouse. Nonetheless, thanks to HKK Group’s flexible offerings, we were able to provide a solution that was perfectly tailored to our needs, which also proved to be affordable.
I would recommend working with HKK Group to anyone looking for comprehensive support in optimizing their warehouse operations.
Katarzyna Ratajczak
Makana Sp. z o.o.
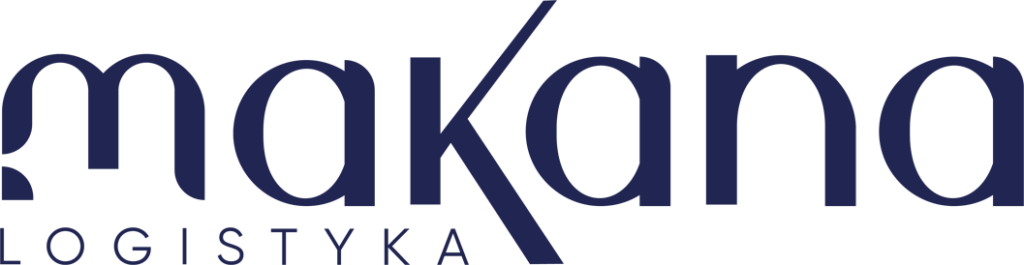
05/
Direct contact
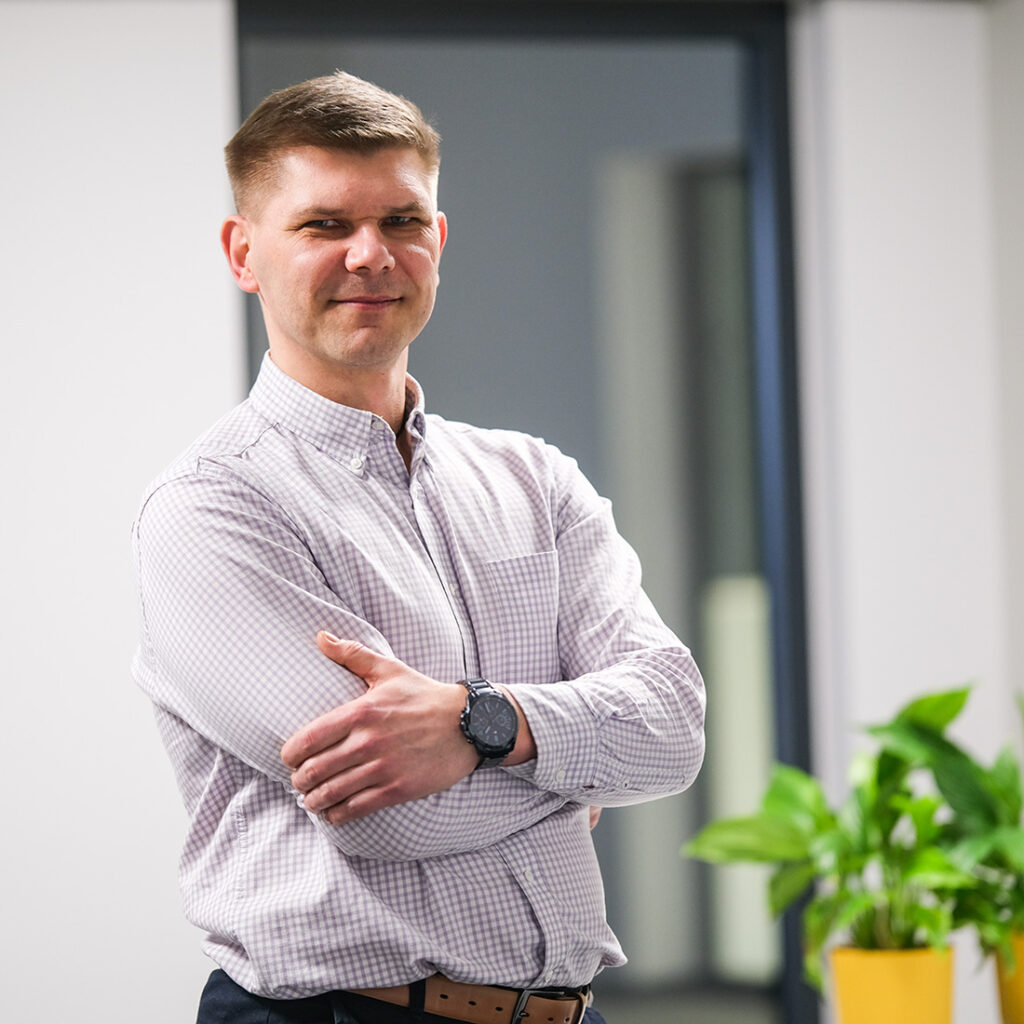