Key information:
How does RFID work?
The method of operation of RFID is not complicated. Users must use RFID reader, as well as RFID tag (also called an RFID antenna or tag). The premise is simple: the reader sends a radio signal in a given area, and the antenna responds with its signal. The entire operation takes a fraction of a second, making the data collected with this technology extremely valuable in terms of process speed. In addition, the whole thing can easily be connected to a WMS warehouse management system.
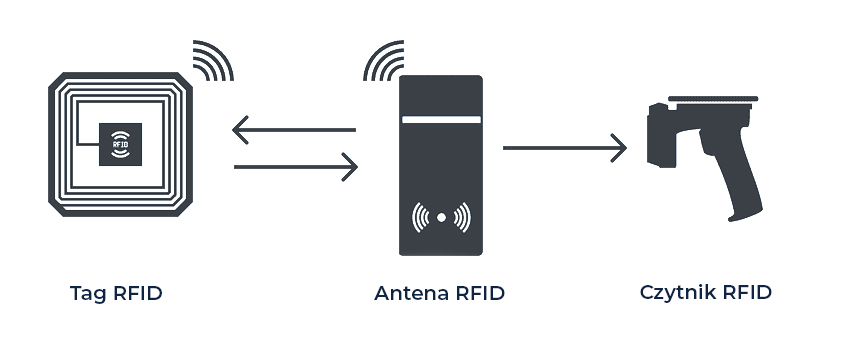
The origins of radio frequency identification
The first research into the use of RFID technology did not quite coincide with the desire to identify specific products. In 1945, Leon Theremin created a listening device that was used by the Soviet Union. The invention retransmitted radio waves to which sound information was added. The sound waves set the diaphragm in motion, which slightly changed the shape of the resonance box, which in turn modulated the reflected frequencies. Although it was a device created for listening only, it is considered the prototype of RFID technology because the passive hardware was activated by sound waves from an external source.
The first true progenitor of modern RFID solutions was a device patented in 1973 by American inventor Mario Cardullo. The passive radio transponder had its own memory of 16 bits. Initial plans called for the invention to be used in highway tolls and vehicle identification, among other applications. It is also worth noting that almost all of the initial applications have been reflected in reality.
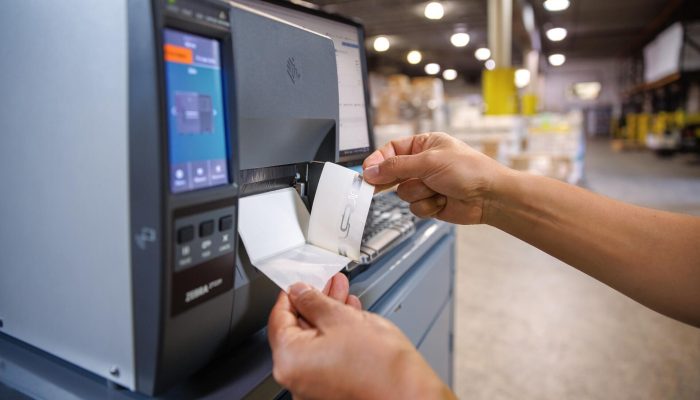
RFID tag
- Passive – passive RFID tags do not require batteries, as they are powered by radio waves sent by the reader. The tag detects the reader’s signal and sends its own signal in response.
- Active – these RFID tags require batteries to power them. A battery is also required for the antenna to send the right signal.
- Semipassive – unlike active RFID tags, semipassive antennas can send a signal thanks to power from the reader, however, they also use external power in the form of batteries.
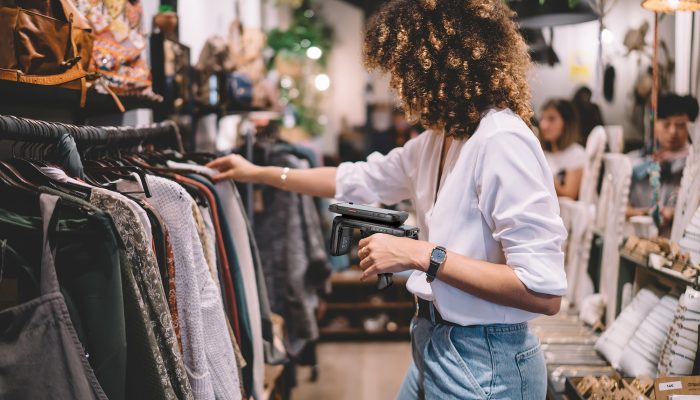
RFID reader
- Stationary – mounted at a specific location, emits a radio signal in the area and receives feedback
- hand-held – can be built into portable equipment, such as a data collector, so it gains mobility
Benefits of RFID implementation
Saving time is the most striking benefit of introducing RFID in an enterprise. As we well know, time is money, so all the seconds needed to identify individual products with a barcode reader can be used in other ways, which translates into an increase in company revenue at the same time.
In theory, RFID technology is not the cheapest, but it will pay for itself in the long run. This has to do with reducing human errors flowing from manual barcode scanning. Since the machines are usually not wrong, the reading of RFID tags is instant and error-free, which means we don’t have to make any correction to the system, and the inventory is complete.
Entrepreneurs will also appreciate the ability to control the production process, as well as the overall supply chain of goods. This fits in with the concept of “traceability,” i.e. the automatic identification of products at each stage of its manufacture and transportation. Traceability makes it possible to keep very accurate records of all parameters and time of a given process, as well as to eliminate products that do not comply with standards or are otherwise unusable.
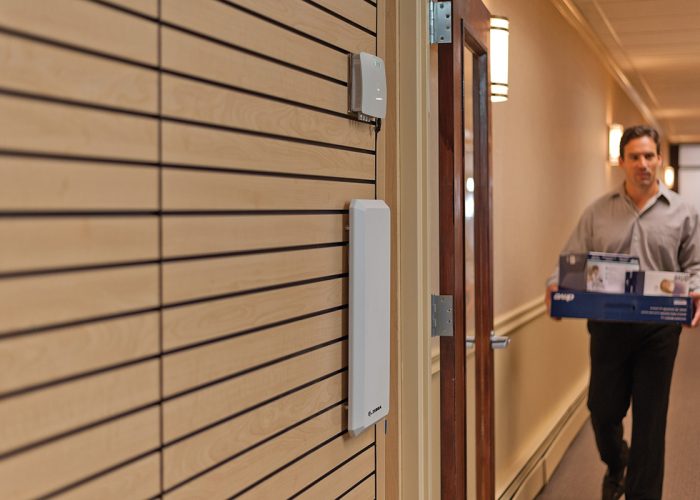
Industries where RFID technology can be used
RFID technology is becoming more prevalent every year in many growing companies. Due to the dynamic environment of today’s logistics, identification time is at a premium. With RFID, we can count on a reading after a few milliseconds, while not wasting time physically taking the product in hand and manually reading the barcode contained on it. In some industries, therefore, it is an extremely desirable solution.
The most popular solution is to identify employees, among others. via special cards equipped with an RFID antenna. Placed in various places in the company, the readers can automatically identify the entering or leaving employee, as well as keep records of working time.
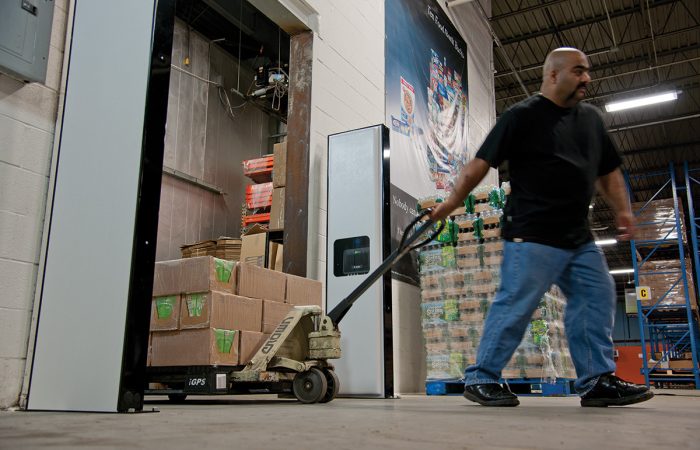
The RFID system will also work well in industries operating under demanding conditions, i.e. wherever conventional barcodes are not a viable option.
Here we mean, for example, conditions during production, such as dust, filings, varnish and painting. An example of this is in the broader automotive industry, where components of automotive parts become varnished, which automatically disqualifies the use of a barcode label.
The biggest advantage of RFID is the ability to fully automate identification. We can install so-called RFID gates that will read tags attached to cars entering the building. In this way, each car, pallet, or even specific product on a pallet, is identified almost upon arrival.
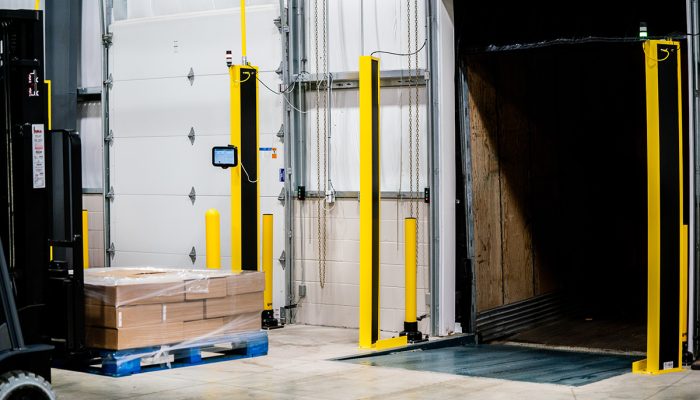
The RFID solution also works well for keeping records of all kinds of containers that return to the company.
If a company transports a particular commodity and uses a container of some kind to secure it, it is usually a reusable container. Many companies face the problem of disappearing containers, which exposes the business to financial losses. With automatic identification using RFID tags and readers, such a problem no longer exists, as we can accurately determine the number of containers.
Examples of RFID usage - our implementations
Implementation of active RFID technology
One of the more interesting implementations carried out by HKK Group is the implementation of a vehicle tracking system at a steel wholesaler’s premises. Facilities of this type are large-scale units consisting of enclosed warehouses and, to a large extent, open-air warehouses. Our client, a leading Polish steel trader and manufacturer of steel components, was struggling with a lack of control over the movement of vehicles inside the warehouse. This factor proved to be very costly, due to the design of carrier fees, which depended in large part on the vehicle’s charging time. As part of the RFID implementation, it was decided to use active tags.
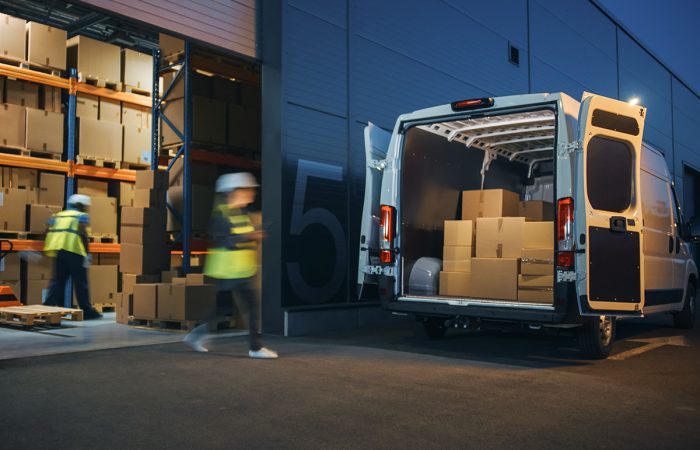
Active RFID tags are reusable, their life expectancy has been set by the manufacturer at up to five years. The tags are placed in small boxes for easy placement behind the windshield of a delivery truck. Drivers of these cars are required to collect an active RFID tag when entering a storage facility and return it when leaving such a facility.
During the implementation, a warehouse map was defined, which forms the basis for tracking the movement of vehicles within the monitored facility. Based on the data from the RFID tag, the system accurately calculates the charging time of the cars and identifies abuse as soon as it occurs. The effect of implementing the RFID system as described, is to significantly reduce charging times, generate measurable savings and increase traffic flow within the facility.
Implementation of passive RFID technology
Passive RFID implementations tend to be much cheaper than active-based implementations mainly because of the The lower cost of the tags themselves. The design of the passive tag which is excited by the radio wave emitted by the RFID reader, is much simpler than the design of an active tag (which communicates with the reader autonomously, without the need for radio wave excitation). Passive RFID implementations are popular wherever there is no way to close the loop to apply reuse of the data carrier.
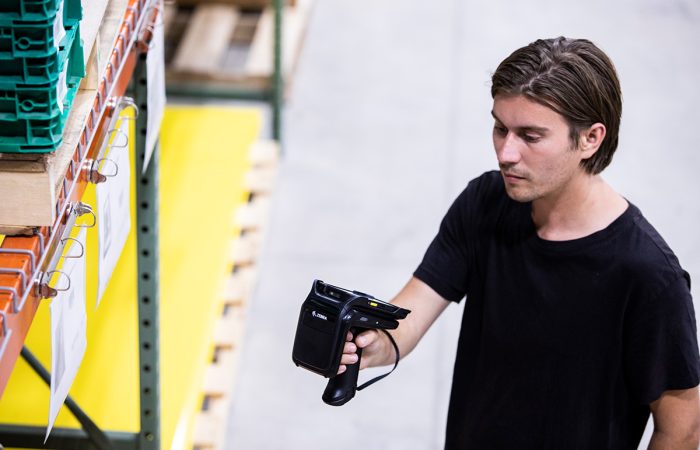
In one of the implementations carried out by our company, we made a production tracking system based on UHF RFID technology. This technology ensures that the tag can be read from as far away as 1.5 meters (and up to 5 meters under optimal conditions). Products that move along the production line are provided with a disposable RFID tag, accompanying each stage of production.
Data on these very stages, combined with an individual tag number, are collected by the production control system. After the manufacturing processes are completed, the RFID tag is placed in the product warranty card (a piece of white bathroom ceramics). In the event of a complaint, the manufacturer can easily trace the history of the product, the type of components from which it was produced and other data important from the perspective of the production process itself.