Key information:
Complete tracking systems function on the basis of a hardware component for marking and reading marks, and software that gives the ability to record all the data collected during the movement of a given product, through the supply chain. In this expert article, we will show you how to design a system that supports tracking the “life” of your product.
Traditional barcode-based traceability system.
If not bar code then other forms of identification (two-dimensional code, RFID and permanent marking).
If the barcode proves insufficient to mark your product (there may be several reasons: from insufficient information contained in the code, to the difficulty of reading it, to the need for more permanent marking), several other marking techniques that can be used in a traceability system will apply.
One technology is the use of a 2D code, or QR code. A 2D code provides greater security for the data contained in its structure. An additional advantage is that it can be read in the case of a partially damaged label.
It is also possible to read the information contained on the carrier without contact. In this case, we are talking about RFID technology, which allows reading by radio.
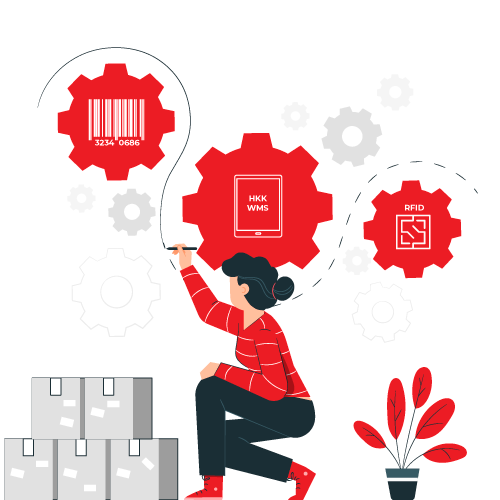
For the most demanding applications, consider permanent labeling. It makes particular sense for marking critical components of equipment or vehicles, which should be identifiable under almost any conditions. Permanent marking is applied using a laser beam emitted by a marking laser. This beam creates a mark in the form of a two-dimensional code on the surface of metal, plastic and many other materials (including organic).
Information system to support the tracking process - a collaboration platform for multiple supply chain participants.
Self-adhesive labels, label printers, barcode readers, marking lasers, or other modern devices supporting automatic data identification are of no use without a proper information system. It is a collaboration platform for all participants in the supply chain of your product. It is such a tool that gives a chance to note every process involved in the turnover of a product. From its production to its final use by the user.
The very architecture of the application, the selection of appropriate hardware to support its operation, and the degree of automation of its functioning is an individual issue, agreed with the customer at the stage of analysis of business needs. Examples include supporting the system with components to automatically read data on production lines, or at specific points along the supply chain.