Key information:
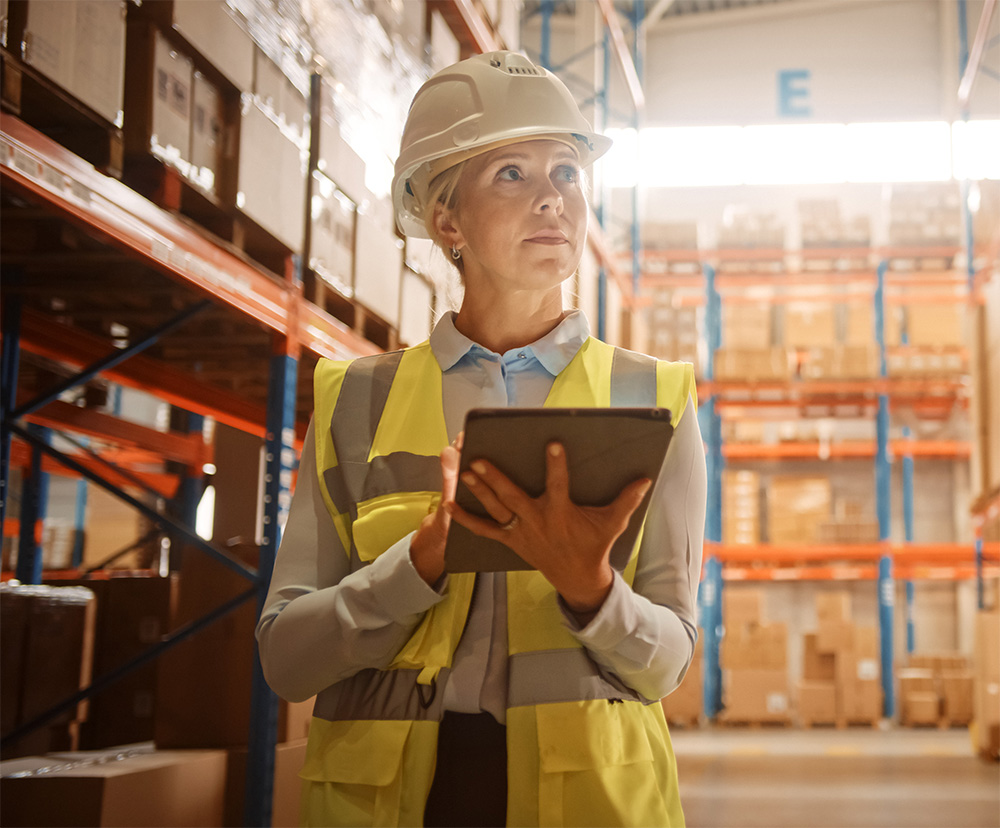
Warehouse Management System
Before answering these questions, let’s revisit the most important information regarding WMS. A warehouse management system ( WMS ) is the heart of a modern distribution center. It encompasses all the elements necessary to carry out any warehouse operation, from the receipt of goods into the warehouse, through storage, to the release of goods.
The WMS system introduces better work organization into the warehouse, supports the efficiency of operations and has the effect of increasing transparency, which in turn has a positive impact on the quality of cooperation with contractors. However, the WMS cannot remain the only element of the modern warehouse ecosystem.
In our opinion, it should also be a good practice to properly label the warehouse with both functional elements (marking zones, storage areas and shelving) and ordering elements (enabling the implementation of the 5S system in the warehouse).
What is 5S labeling and how to implement it in the warehouse?
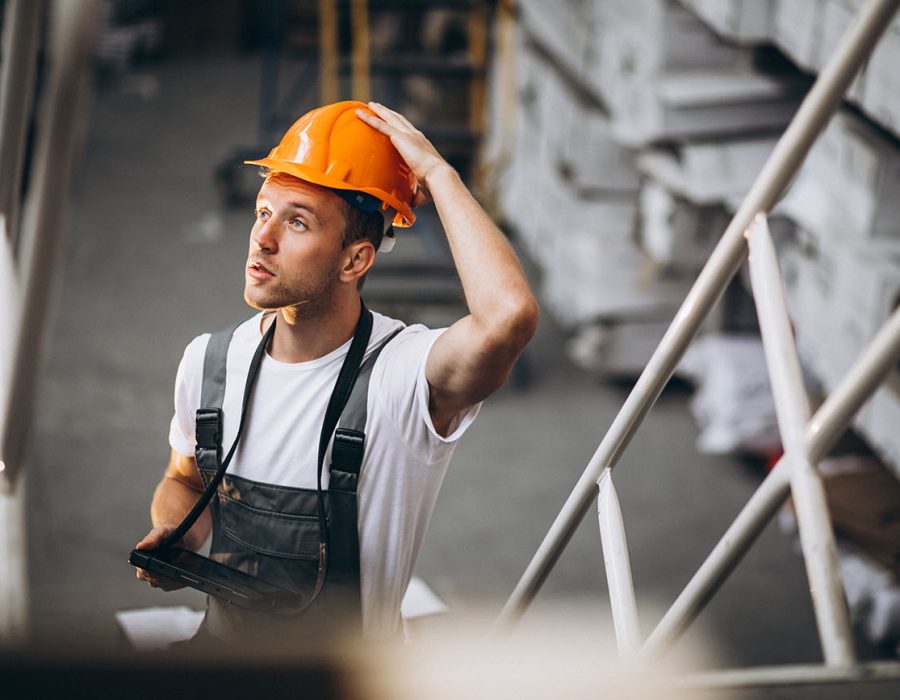
01/ Sort
First, determine what is needed and what is unnecessary (SORT).
In this step, the most important thing is to verify the current state of your infrastructure. It is worthwhile to look at the organization of each workstation, analyze the tools, devices that support the work, and all areas and places used for storing goods. The end result of such an analysis should be a decision on what is actually needed for the daily operation of the company, and what is not needed.
It may be that certain items of warehouse equipment seem necessary, but there is no certainty as to how often they will be used. Thus, it is worthwhile during the initial verification to create a “reserve” zone in order to later determine the necessity of the item. All items subjected to such analysis should be properly marked with a red label or tag of the same color.
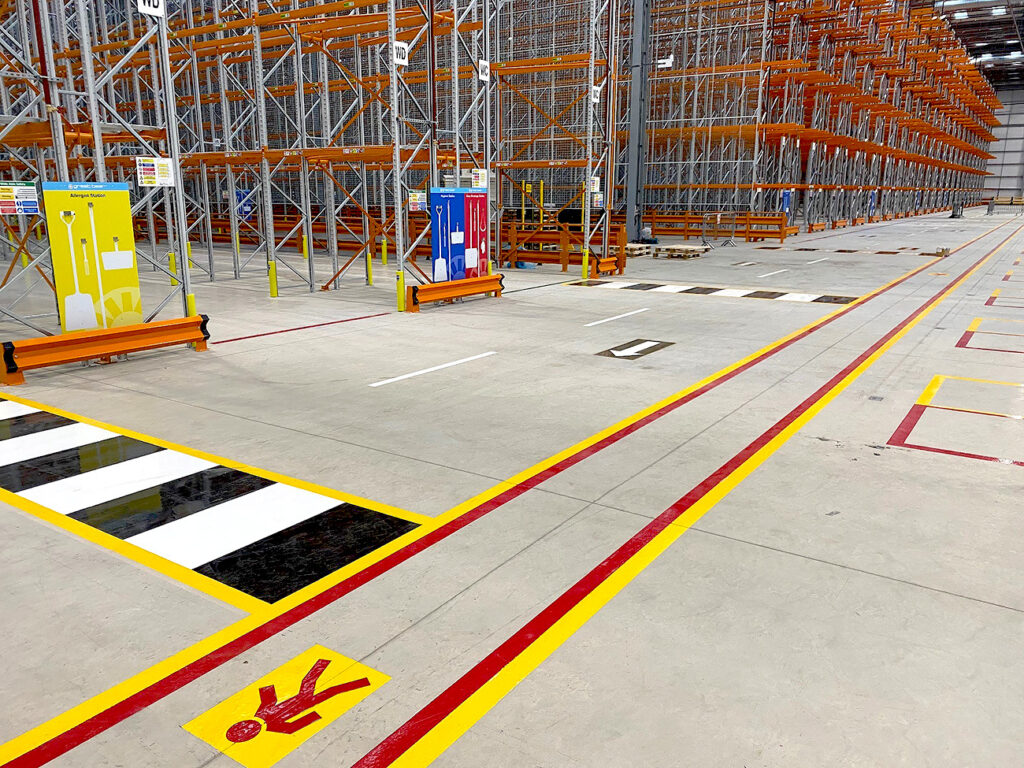
02/ Set in order
Step two in 5S is the systematization element (SET IN ORDER).
After eliminating unnecessary elements, it is easier to control the processes taking place in the logistics space. In the systematization phase, it is worth taking care to analyze who uses what, with what frequency, in what way and for what purpose, so that work is done in accordance with the lean philosophy without generating losses in the form of reduced efficiency.
Tasks from the systematization phase are worth conducting in working groups, involving employees dealing with real-world challenges on a daily basis. The result of the work in this phase can be the delineation of new optimized transport routes (lining them with special tapes), the use of signage elements in the form of special 5S boards or the use of shadow boards designed to hold items of logistics equipment.
Our company (HKK Group HIT-Codes) has been optimizing logistics, production logistics and manufacturing processes for almost 30 years.
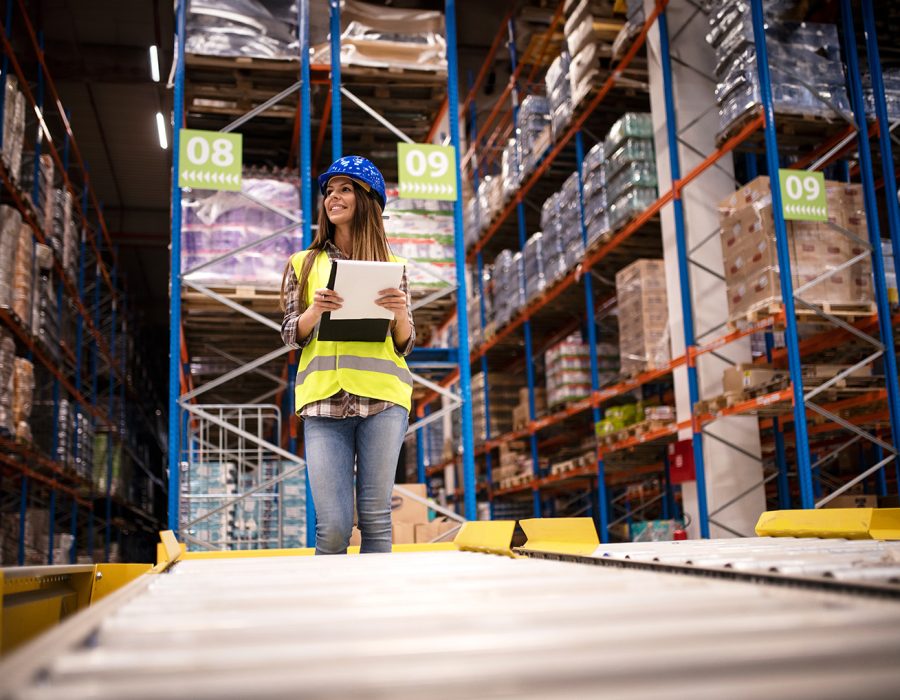
03/ Shine
Step three of the 5S system is the cleaning element (SHINE).
The cleaning element is not just about cleaning accompanying the introduction of the system itself, but also about developing a method to permanently keep the storage space in good order.
As part of this phase, it is necessary to analyze the work of each warehouse operator, get acquainted with his work area and decide what cleaning work should be part of his duties. As part of the decisions made in the area in question, it is also necessary to ensure access to cleaning tools, their optimal placement, as well as the definition of responsibility regarding their maintenance.
The aforementioned shine area tasks can be helped by the aforementioned shadow boards, but also by dry-erase boards that systematize the planning of housekeeping tasks.

04/ Standard
Step four standardization (STANDARD).
This is perhaps the most important step in introducing 5S in the warehouse logistics area. After the changes, our warehouse looks different, there is order in it, unnecessary items have been removed. The standardization process will ensure that the cleanup effort is not an effort comparable to pre-Christmas cleaning. As part of this step, it is worth creating job instructions and communicating them transparently.
It is also worth defining the procedures associated with almost every warehouse activity performed by multiple employees and ensuring that they are properly visualized with signage. Properly working through standardization tasks will make new habits and procedures a matter of course.
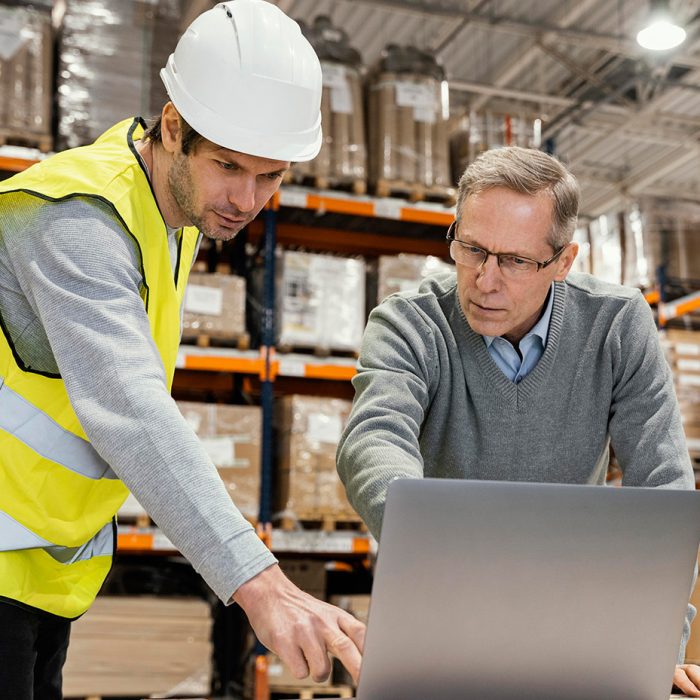
05/ Sustain & Safety
Step five maintenance and self-discipline (SUSTAIN).
This is the final step in the standard 5S approach. As part of this step, it is worth ensuring that a subsystem of training (introductory and sustaining) is established for staff. It is also worth providing communication tools related to the 5S system. All of these elements are designed to ensure that the crew maintains a high level of awareness and motivation, so that the newly introduced rules become a habit and a natural part of working in the warehouse
Eye on Safety (SAFETY).
An extension of the 5S method is sometimes the 6S method, where safety issues are treated as elements of special interest and a separate subsystem is created for them. As part of the safety effort, all job risks should be analyzed, as well as leaning into each tool, machine or communication path. Any items carrying any safety risk should be labeled, described, and their users properly instructed.
HKK Group's unique competence in comprehensive consulting for logistics.
Our company (HKK Group HIT-Codes) has been optimizing logistics, production logistics and manufacturing processes for almost 30 years. As part of our activities, we not only implement IT systems for managing these areas, but also marking systems for warehouses, production halls, offices, or public places in accordance with the 5S standard.