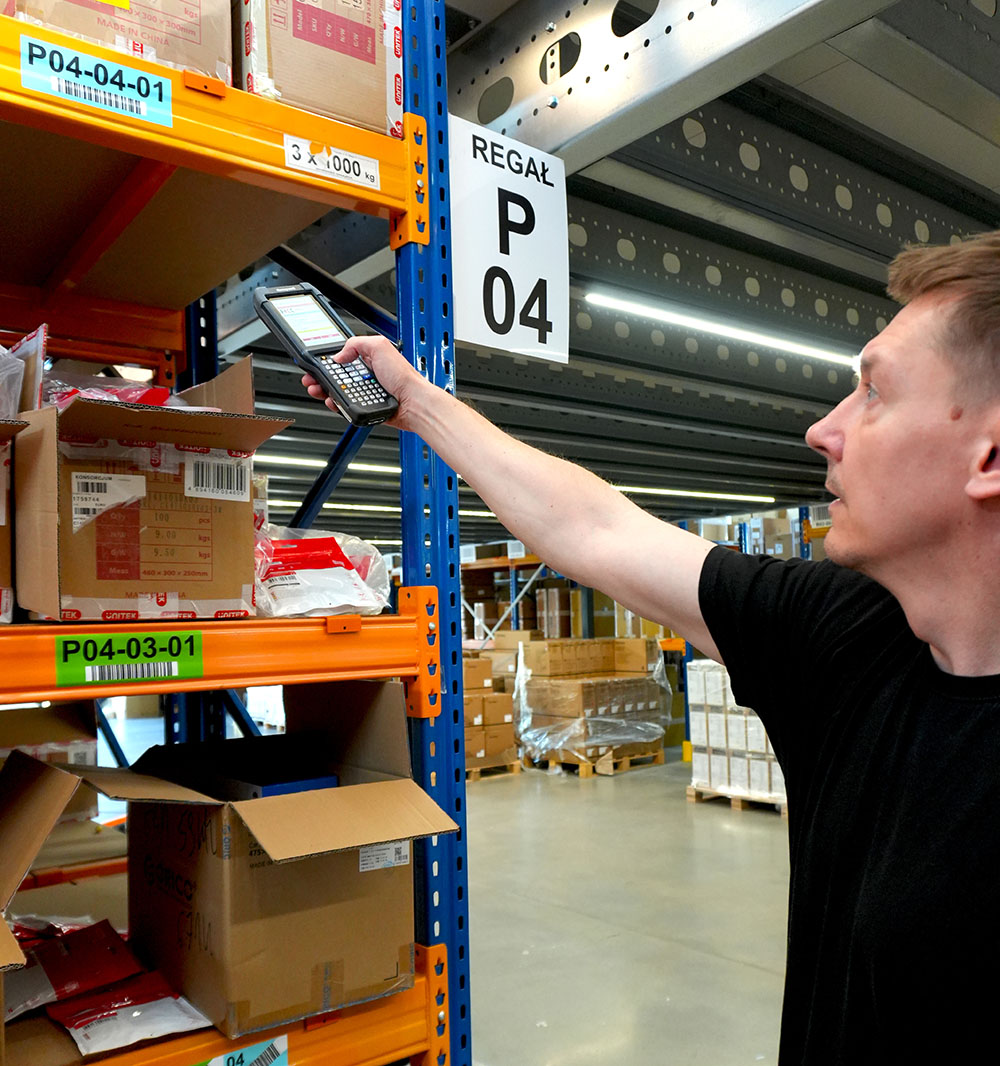
WMS as the foundation of a modern warehouse
The first and most important step toward warehouse automation is the implementation of a WMS, a warehouse management system that acts as the “brain” of a modern distribution center.
The WMS system allows you to comprehensively manage all stages of warehouse work: from the receipt of goods, through their storage and order picking, to the release of goods to the customer. In daily operation, it is supported by automatic identification technology – bar codes, 2D codes or RFID – enabling instant identification of goods, storage locations and shipping packages.
Advantages of implementing a WMS:
-
Accelerate warehouse operations by up to 30%
-
Increase storage capacity in limited space
-
Reduction of errors and mistakes in order processing practically to zero
In order for a WMS to work efficiently, warehouse signage and automatic identification devices such as:
-
barcode scanners (code readers),
-
mobile terminals (data collectors),
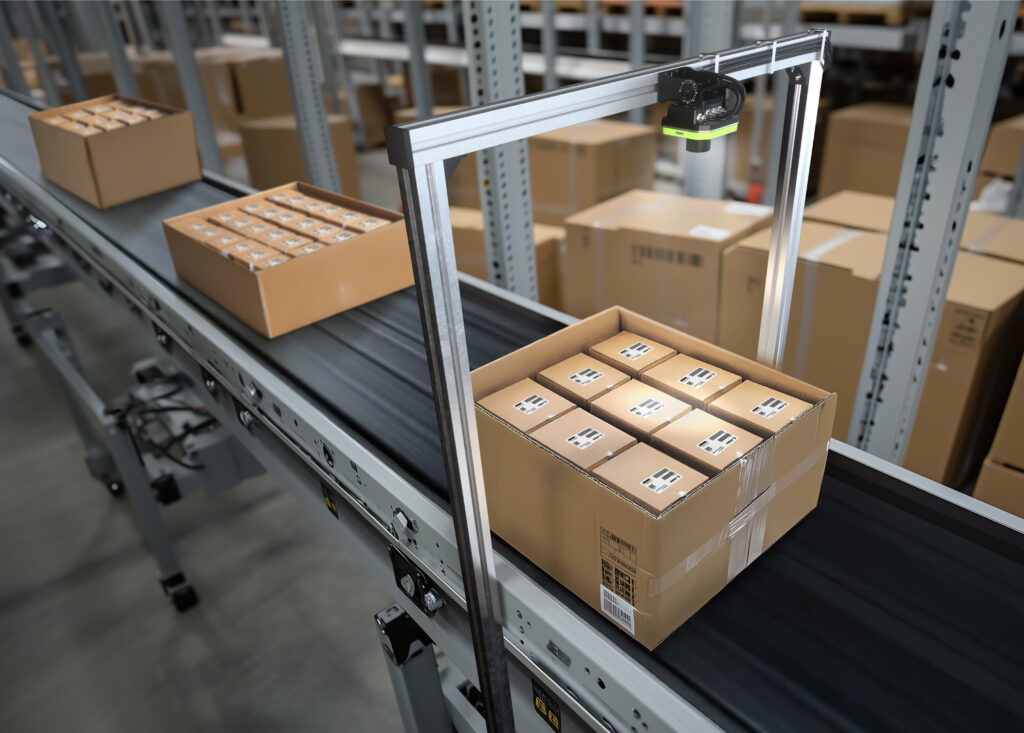
Additional systems to support warehouse operations
A WMS is the foundation. In order to further optimize warehouse operations, it is worth considering the implementation of additional supporting systems that will increase the accuracy and speed of logistics handling. Based on our years of experience, we recommend, among others:
-
Automatic label reading systems – significantly improve the process of receipt and release of goods, eliminating human errors.
-
Dimensioning systems in logistics, such as Cubiscan – allow for accurate product dimensioning and optimization of so-called master data.
-
Automatic label applicators (print&apply) – enable automatic printing and application of labels to pallets and bulk packages during the shipping process.
The use of these solutions saves precious minutes at each stage of the warehouse operation, which translates into real process savings on an annual basis.
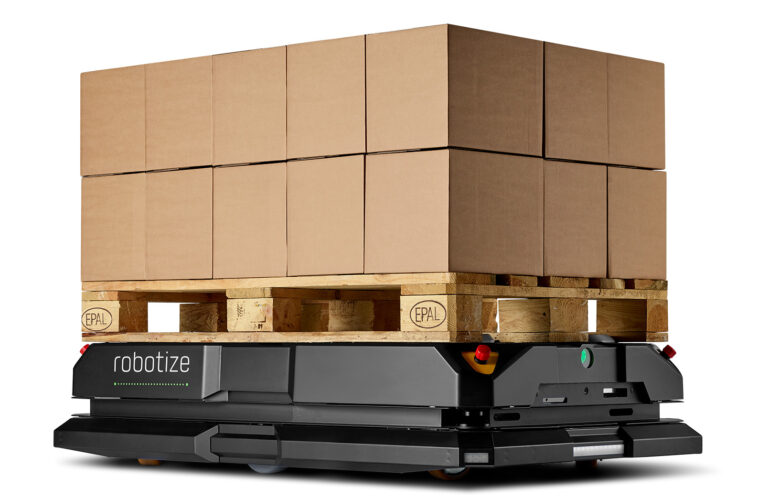
Logistics robotics - a new era of material handling
Another step toward full automation is the implementation of AMR (Autonomous Mobile Robots), which are revolutionizing internal transportation in warehouses.
AMR robots are a development of AGV (Automated Guided Vehicles) technology. The main difference lies in the way they navigate – AMR robots use SLAM (simultaneous localization and mapping) technology, which allows them to autonomously create a map of the storage space. Thanks to cameras and sensors, AMRs can detect obstacles in real time and dynamically adjust their route.
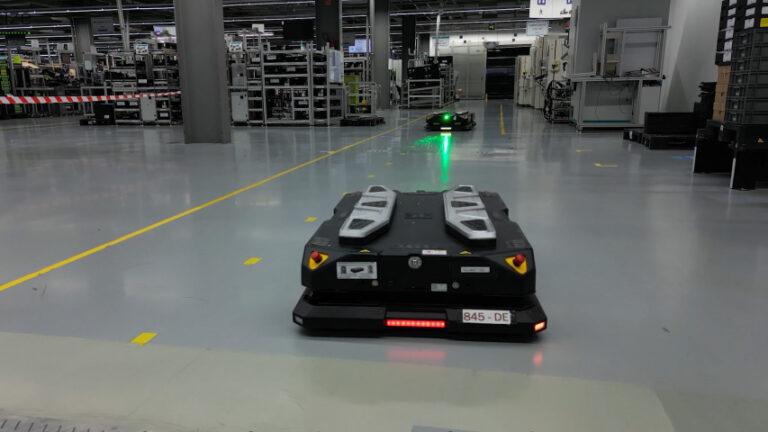
Advantages of implementing logistics robotics
Advantages of AMR robots:
-
Quick implementation and adaptation to the space
-
Automatic response to changes in the environment
-
ROI after just 12-18 months
HKK Group’ s offerings include GoPalpallet robots from Robotize, as well as P35platform robots from the same brand – ideal for carrying picking carts.
We encourage you to test these solutions in your own warehouse or manufacturing space and see how they can support your logistics.