Key information:
As an organization specializing in handling warehouse logistics and production logistics processes, we feel competent to suggest how to carry out logistics investments so that they can withstand the passage of time and become a center for generating competitive advantage.
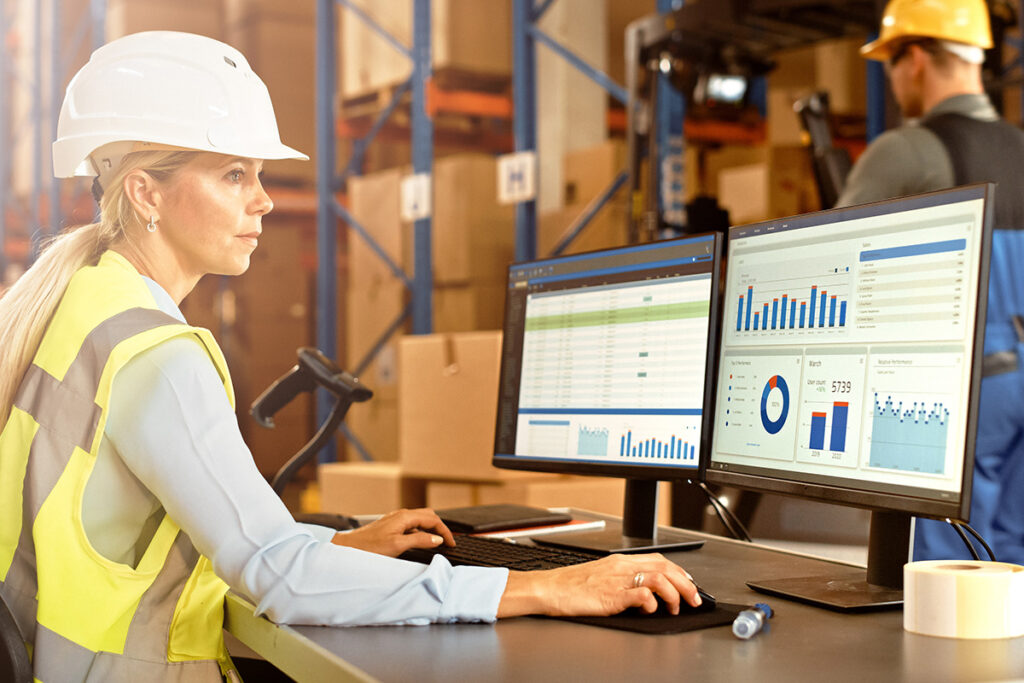
The WMS is the brain of the modern warehouse.
The degree of complexity of modern warehouse operations does not allow their implementation without the support of an IT system. The most effective solution to support warehouse operations is a WMS (warehouse management system) class system. An IT solution of this type comprehensively manages all operations in the warehouse from the entry of goods into the warehouse, through their storage, to their release outside the warehouse.
In order to carry out these tasks efficiently, the WMS system bases its operation on barcode technology, and increasingly on 2D code technology. It is barcodes and automatic data identification devices(data collectors, code readers, self-adhesive label printers), which make it possible to quickly read information about the product, its storage location, deliveries or other important processes taking place in the warehouse.
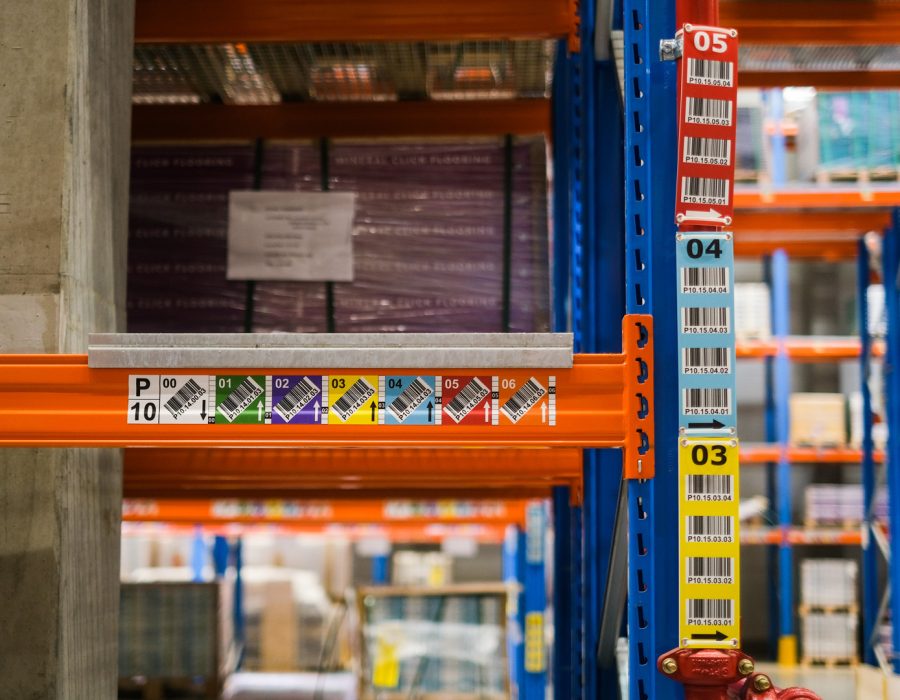
What happens before, or during, the implementation of a WMS?
Before implementing a WMS, it is worth taking care of a few elements that affect its efficiency. These are primarily:
- functional and system labeling of the warehouse,
- Ensure consistency and completeness of input data(master data).
Among other things, warehouse labeling uses. plates informing about aisle numbers, or system labels indicating the exact location of goods on the rack. Such labeling will make the distribution center much more orderly, and the operator’s work will become faster and more efficient.
It is extremely important to take care of the quality of product input data. This primarily involves standardizing the naming of commodity indexes and enriching them with parameters related to dimensions and weight. The process of obtaining such data can be automated using Cubiscan dimensioning equipment.
In the near future, it will be common for robots to support process execution by performing repetitive work, such as carrying goods from the receiving area to storage areas. It is worth taking care to enable fast and inexpensive integration between WMS and autonomous robot systems.
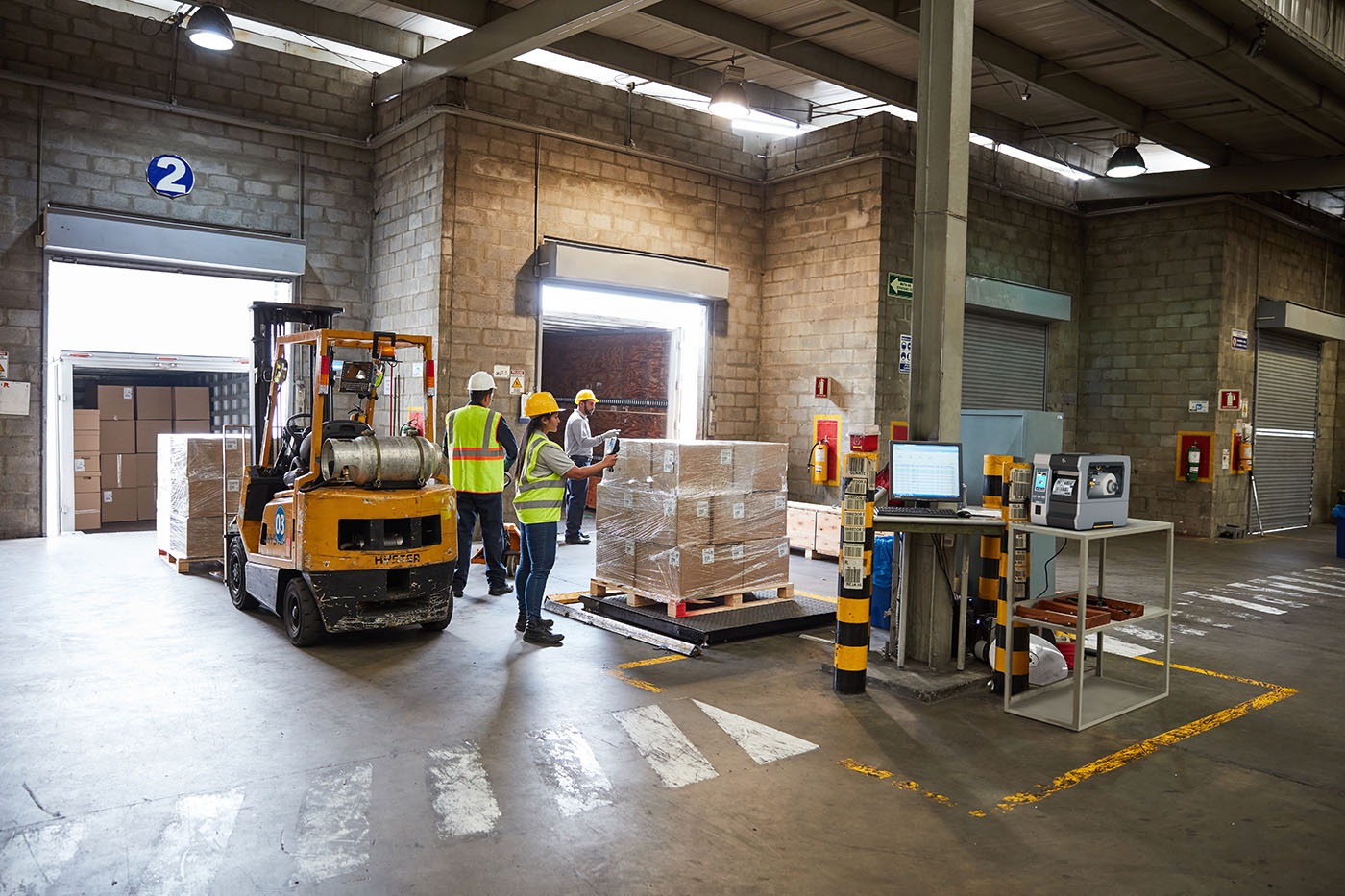
How to streamline the process of receiving goods into the warehouse?
When designing a complete, adaptable warehouse logistics support system, it is worth starting with the first in the sequence of processes, which is the receipt of goods into the warehouse. At this stage, it is worth designing a solution based on GS1 standards, so that the execution of admissions takes place automatically, by reading the code.
This will make it possible to take stock of the goods, along with automatic determination of all additional data, such as expiration dates, serial numbers, etc. In the case of receiving goods in standardized packaging (for example, pallets or cartons), it is worth thinking about an automatic unloading system that not only transports the goods from the delivery truck, but also reads the contents of the code and directs the received goods to their place of storage.
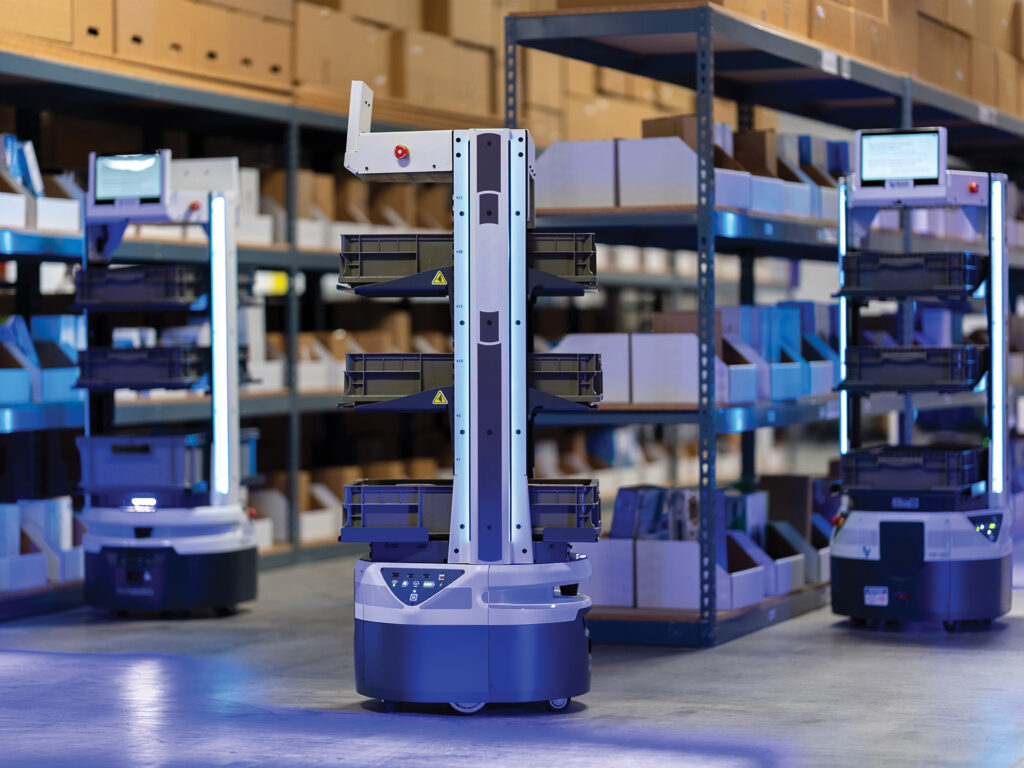
Storage of goods in a modern warehouse.
A modern, future-proof warehouse should be open to the use of elements that streamline or automate the storage process.
In the near future, it will be common for robots to support process execution by performing repetitive work, such as carrying goods from the receiving area to storage areas. It is worth taking care to enable fast and inexpensive integration between WMS and autonomous robot systems .
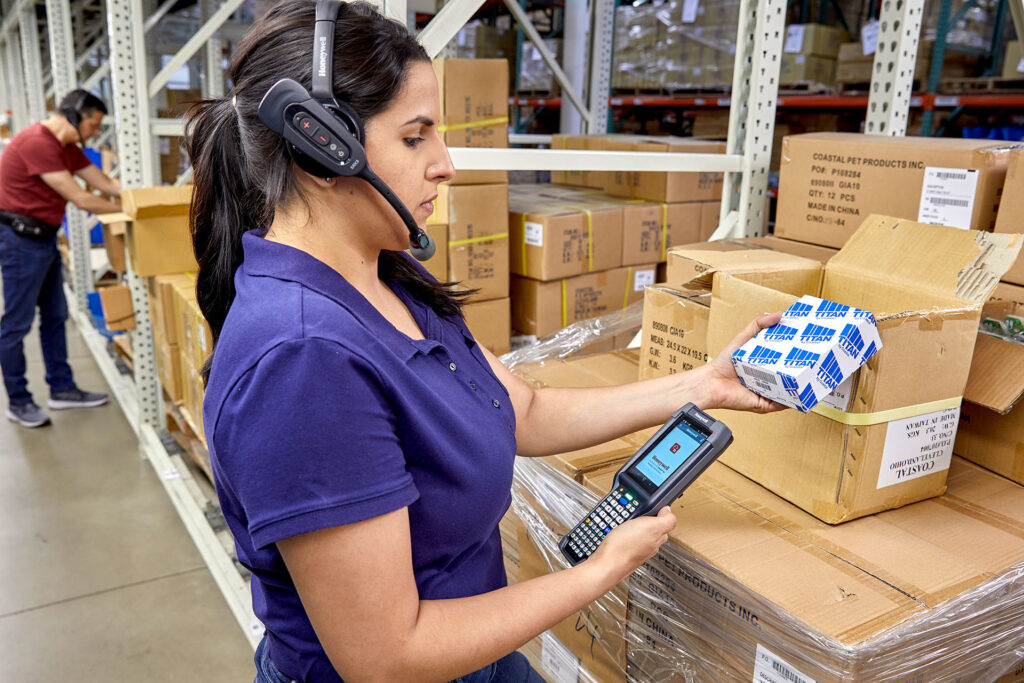
Picking of goods and their release.
The last of the basic warehouse logistics processes is picking, which is the preparation of goods for shipment under a specific customer order. In order to optimize this process, it is worth ensuring that our system is equipped to handle modern picking methods.
These include multi order picking (particularly useful in the picking process for the e-commerce sector), or
voice picking
(voice picking used in the picking process of so-called general cargo).
As for the shipping process, a modern warehouse should have the ability to integrate with almost any courier system to quickly print waybills and courier labels.
HKK Group - Your Logistics One Stop Shop.
For years, our company has been engaged in providing comprehensive services related to the design and implementation of automatic identification systems. We have helped many times to increase the turnover of more than one organization by implementing a system consisting of the components we mention in this article.
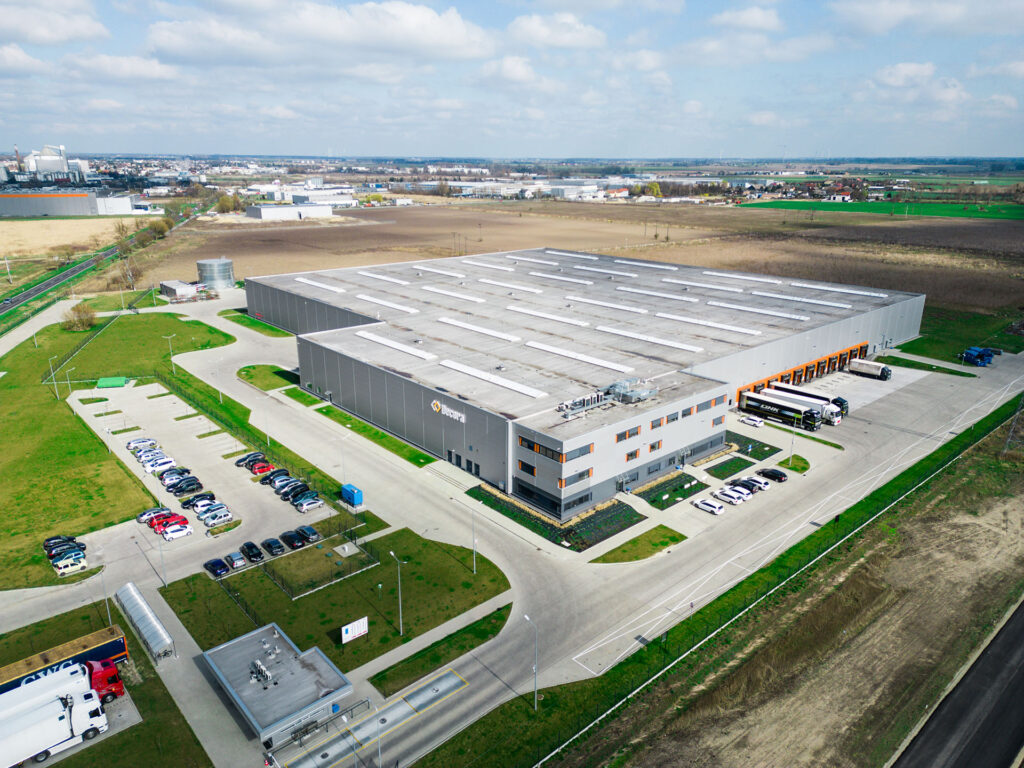
Case study
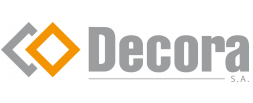
Together with our client, we adopted the goal of implementing a comprehensive and consistent signage system as an integral part of the infrastructure of a modern distribution center.