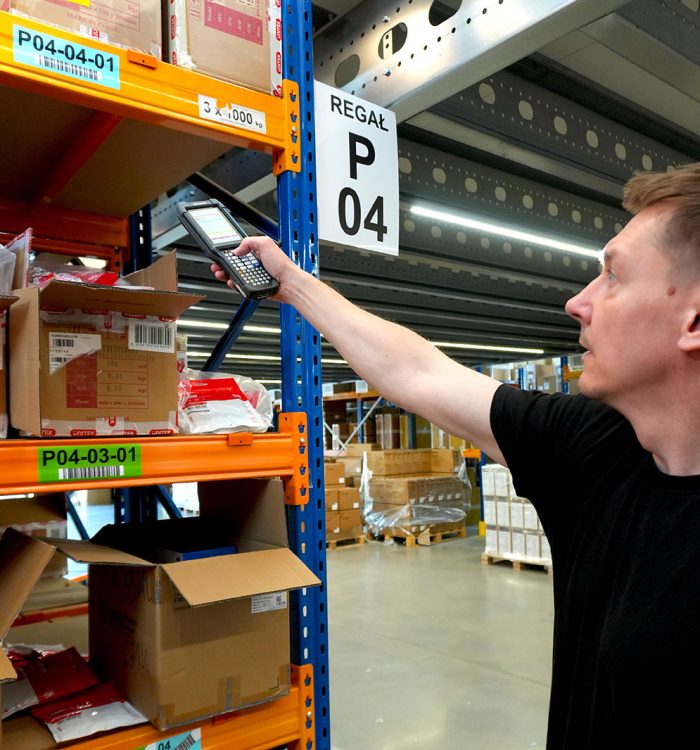
Areas of operation of the WMS system
A WMS class system is a comprehensive solution, supporting all key areas of work of a modern warehouse. For a better understanding, it is worth dividing the WMS functionality into main process areas:
Warehouse goods receipt area
The WMS supports the goods receipt process by assigning a unique registration number to each smallest, countable batch of goods. Reception can take place both in an advised manner (automatically or through a web portal) and ad-hoc.
Warehouse storage area
WMS assists users in selecting the best place to store products. In doing so, it takes into account constraints, dimensions, weights and rotation frequency. The use of appropriate algorithms makes it possible to increase the efficiency of warehouse space use by up to 30%.
The area of picking goods for orders
The system optimizes the path of picking goods, selects the right packaging and controls the correctness of picking, minimizing the risk of errors.
The goods release (shipping) area of
WMS allows automatic generation of shipping labels and communication with courier systems. It also manages additional requirements related to quality, packaging and sends notifications to recipients.
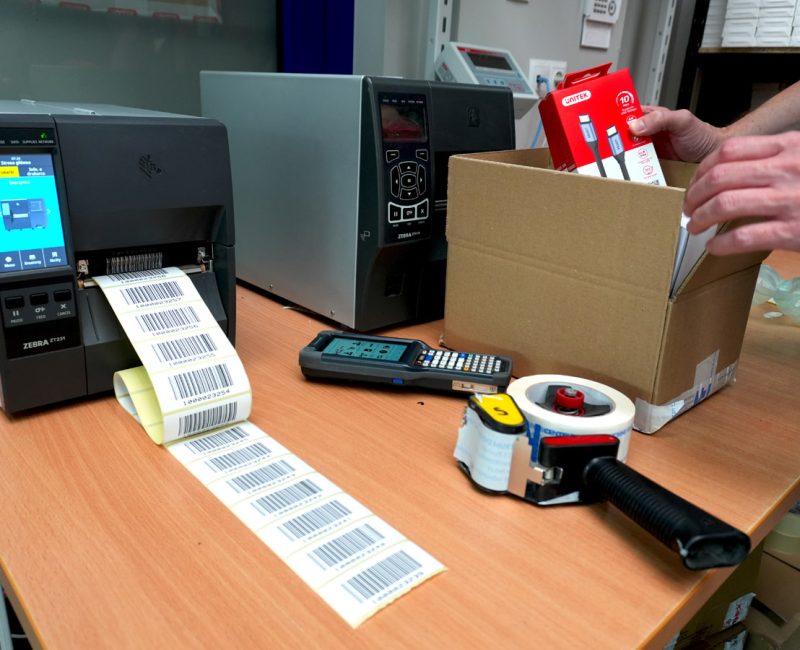
What is needed to make a WMS system work?
In order for a WMS to operate smoothly and efficiently, the right infrastructure is essential:
stable Wi-Fi network in the warehouse area,
self-adhesive label printers For printing registration and courier labels,
data collectors / mobile terminals For warehouse workers,
barcode scanners (manual, cart, automatic)
marking of storage areas, shelving and storage areas.
It is also worth considering supporting elements that, although not essential, significantly improve efficiency:
Cubiscan – Product sizing equipment to enhance the quality of master data,
AMR mobile robots – automating the transport of pallets and goods after picking, working with the WMS system.
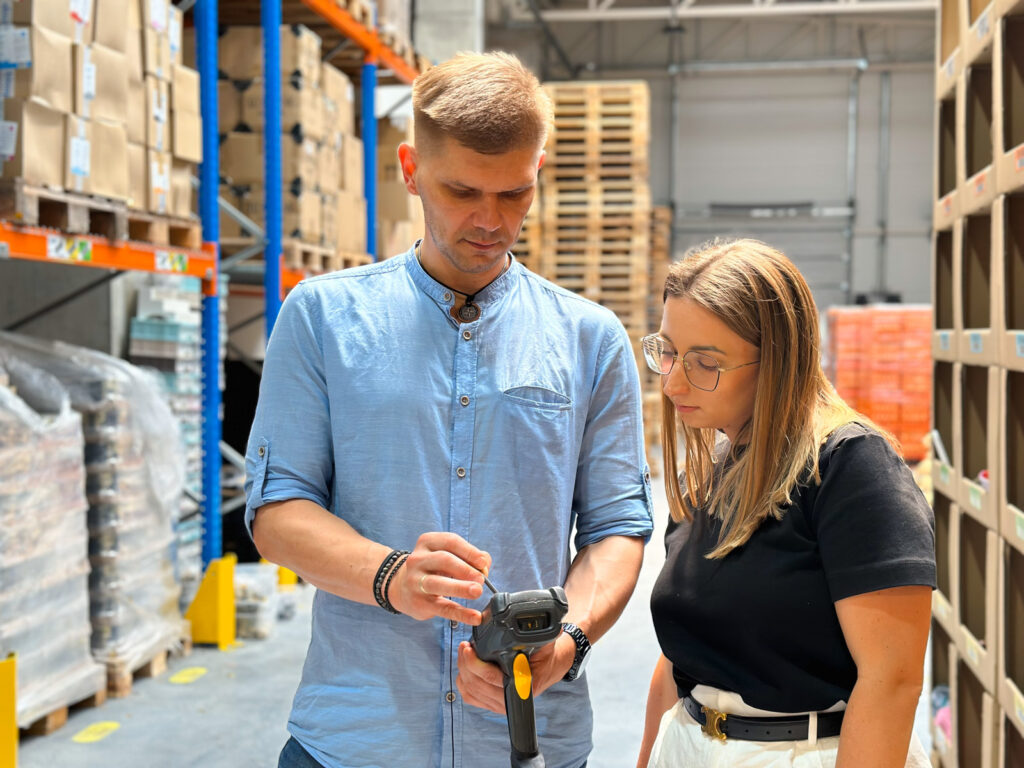
WMS implementation process
Implementation of our proprietary WMS can take from a few weeks to as long as several months – depending on the degree of integration with external systems.
The implementation process follows the ATOM methodology:
Asses – evaluation of implementation goals,
Transform – customization of the WMS system to meet the customer’s needs,
Own – handing over a fully functional system,
Measure – measure the effects against the set goals.
The effects of the implementation include a reduction in warehouse errors and a 30-40% increase in process efficiency. HKK offers two solutions:
Blue Yonder WMS – A leading warehouse management system,
Digit.IO WMS – A proprietary solution with the ability to expand with an MES module for production management.